Summary:
Why Flat Belt Conveyors Are Essential for Efficient Material Handling
The Key Benefits of Using Flat Belt Conveyors in Material Handling
How Flat Belt Conveyors Improve Workplace Safety
Key Features to Consider When Choosing a Flat Belt Conveyor
Flat Belt Conveyors vs Other Conveyor Types: Why Flat Belts Stand Out
The Key Benefits of Using Flat Belt Conveyors in Material Handling
Flat belt conveyors are a cornerstone of modern material handling systems across a variety of industries. They offer a simple yet effective solution for moving goods from one point to another, and their benefits go far beyond just transporting materials. By enhancing efficiency, reducing costs, and improving versatility, flat belt conveyors have become indispensable in operations ranging from manufacturing plants to warehouses. Let’s explore the key benefits of incorporating flat belt conveyors into your material handling system.
Increased Efficiency in Material Transportation
One of the most significant advantages of flat belt conveyors is the efficiency they bring to material handling. These systems streamline the transportation of materials, enabling them to move quickly and smoothly from one part of the production process to another.
How Flat Belt Conveyors Streamline Production Lines
In a fast-paced production environment, time is money. Flat belt conveyors help reduce downtime between production steps by maintaining a continuous flow of materials. The uniform speed and predictable movement of the flat belt ensure that products move seamlessly from one station to the next, reducing the need for manual handling and minimizing delays in the production line. This constant movement helps meet production goals and tight deadlines, especially in industries like automotive manufacturing and packaging.
Reducing Manual Labor and Minimizing Human Error
Flat belt conveyors significantly reduce the need for manual labor in material transportation. Instead of workers having to physically move materials, the conveyor system takes on the heavy lifting. This not only frees up human resources for more critical tasks but also minimizes the chances of human error. With human error often contributing to inefficiencies, damage, and costly mistakes, automated conveyor systems can increase the overall accuracy and reliability of the production process.
Enhancing Throughput and Workflow
One of the key performance indicators for any material handling system is throughput – how quickly materials can be processed and moved through the system. Flat belt conveyors can dramatically increase throughput by ensuring a smooth and consistent flow of products. Whether it’s a continuous flow of raw materials, a series of assembly tasks, or finished goods moving to packaging, the conveyor ensures that everything progresses without interruption. The ability to handle large volumes without compromising speed is essential, especially for high-demand industries like food processing or e-commerce fulfillment centers.
Cost-Effective Solution for Material Handling
While investing in a conveyor system may require an upfront cost, the long-term savings and return on investment (ROI) make flat belt conveyors a cost-effective choice for many businesses.
Lower Maintenance Costs Over Time
One of the reasons why flat belt conveyors are so cost-effective is their low maintenance requirements. Unlike other types of conveyors that rely on complex components or mechanisms prone to wear and tear, flat belt conveyors have fewer moving parts. The simplicity of their design reduces the likelihood of frequent breakdowns and costly repairs. With proper maintenance, such as regular cleaning and belt inspections, flat belt conveyors can run for years with minimal intervention, helping companies save on costly repairs and downtime.
Energy-Efficient Operations Compared to Other Conveyor Types
Flat belt conveyors are also known for their energy efficiency. Because the belt is typically powered by a single motor and moves at a consistent speed, they require less energy to operate than more complex systems, such as roller or chain conveyors. In industries where conveyor systems are running continuously or in shifts, these energy savings can add up significantly over time. Reduced energy consumption not only helps to cut operational costs but also contributes to a company’s sustainability goals by reducing its carbon footprint.
Durability and Long-Term ROI
The durability of flat belt conveyors further enhances their cost-effectiveness. Made from strong materials such as PVC, rubber, or polyurethane, flat belts are designed to withstand the wear and tear of constant use. As a result, businesses get a high ROI from the equipment as it can last for years without needing significant replacements. Additionally, the modular design of many flat belt conveyors makes it easy to replace individual sections of the belt, allowing for cost-effective repairs without needing to replace the entire system.
Versatility Across Different Industries
Another reason flat belt conveyors are so widely used is their remarkable versatility. These conveyors can be adapted to suit the needs of virtually any industry, from food processing and pharmaceuticals to automotive and e-commerce.
Manufacturing and Assembly Lines
In manufacturing environments, where the speed and reliability of the production process are crucial, flat belt conveyors are often used to transport parts through assembly lines. Their ability to handle materials of varying shapes and sizes—whether small components, large assemblies, or packaged goods—makes them an ideal choice for industries such as electronics, automotive, and consumer goods manufacturing. They can be customized to include features like incline/decline angles, curves, and various surface types, making them adaptable to different types of materials.
Food and Beverage Industries
The food and beverage industry, with its strict hygiene standards and need for precision, benefits greatly from the use of flat belt conveyors. The smooth, continuous surface of the flat belt reduces the risk of contamination, ensuring that products move through the system without debris or dirt accumulating. Additionally, these conveyors can be easily cleaned, which is a crucial factor in food processing and packaging. The ability to handle delicate items, such as packaged goods or glass bottles, without damaging them makes flat belt conveyors an essential part of this industry.
Packaging and Logistics
In the logistics and packaging sectors, flat belt conveyors are used to efficiently move packages from one station to another, often as part of a larger automated system. Their smooth surface and ability to be customized for different load sizes make them ideal for transporting boxes, bags, or other packaged items. With the rise of e-commerce, where quick turnaround times are essential, flat belt conveyors play a key role in helping businesses meet the demand for faster shipping and efficient order fulfillment.
How Flat Belt Conveyors Improve Workplace Safety
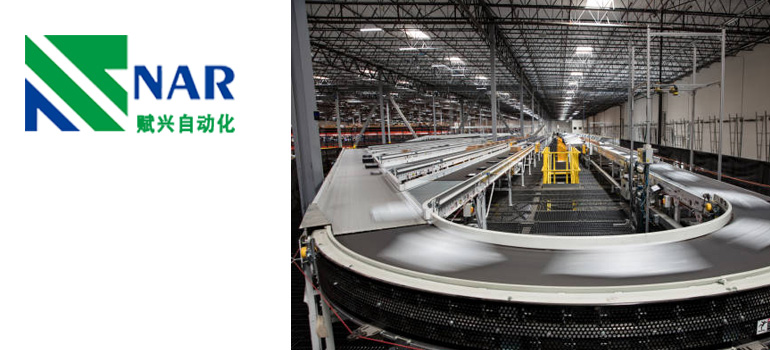
Workplace safety is a critical concern for every industry, especially in environments where heavy machinery, moving parts, and large volumes of materials are involved. Flat belt conveyors, commonly used in manufacturing, packaging, and material handling operations, offer significant safety advantages that help reduce workplace accidents, protect employees, and ensure smooth operations. Here’s how flat belt conveyors contribute to a safer working environment:
Minimizing Workplace Accidents and Injuries
One of the main reasons flat belt conveyors are favored in industrial settings is their ability to reduce the likelihood of accidents and injuries.
Smooth, Continuous Operation Reduces Sudden Movements
Unlike conveyors with more complex mechanisms, such as roller conveyors or chain conveyors, flat belt conveyors provide a smooth, continuous surface for materials to move along. This design minimizes jerky or sudden movements that can cause items to shift unexpectedly, potentially leading to accidents or injuries to workers. A flat, stable surface allows materials to stay in place, reducing the risk of products falling or spilling, which could result in dangerous slips or trips.
Prevention of Material Spillage and Contamination
In industries such as food processing, pharmaceuticals, and chemicals, material spillage can pose a serious safety hazard. Flat belt conveyors, due to their uniform surface, help ensure that products stay securely in place, preventing them from spilling or contaminating other areas. This is especially important when transporting materials that are hazardous or delicate, such as liquids, fine powders, or small parts. By keeping materials contained, flat belt conveyors reduce the risk of workplace contamination and exposure to dangerous substances.
Reducing Manual Handling Risks
Manual handling of materials is one of the leading causes of workplace injuries, such as strains, sprains, and musculoskeletal disorders. By automating material transportation with a flat belt conveyor system, the need for manual lifting, carrying, and moving of heavy items is significantly reduced. Workers are less likely to sustain injuries caused by repetitive or physically demanding tasks, leading to a safer and healthier work environment.
Improving Control and Stability
Flat belt conveyors offer a level of control and stability that enhances safety in a variety of ways.
Stable Movement of Materials
A flat belt provides consistent, stable movement for materials, which is especially important when handling delicate or fragile items. Whether it’s fragile glass bottles in a bottling plant or small parts in an assembly line, the smooth, stable movement of flat belt conveyors reduces the risk of these items being damaged or causing accidents. Stable material movement also helps ensure that operators can control the flow of materials without worry that items might get caught or become misaligned.
Less Risk of Product Damage During Transit
In many industries, particularly in electronics, food production, and packaging, the risk of damaging products during transportation is a significant concern. Flat belt conveyors are ideal for moving sensitive materials because they provide a smooth, controlled surface, minimizing the risk of bumps, knocks, or jolts that could damage the items. This level of control helps not only improve workplace safety but also maintain the quality and integrity of products being transported.
Stable Surfaces for Fragile or Irregularly Shaped Products
Flat belt conveyors are especially effective for handling irregularly shaped or lightweight materials. The smooth surface and controlled environment help prevent products from shifting, falling, or becoming misaligned, which can often happen when handling products on conveyors with gaps or uneven surfaces. By keeping these materials stable, flat belt conveyors reduce the chances of product-related accidents or injuries.
Automating Hazardous Tasks
Automation plays a key role in improving safety by removing workers from high-risk or physically demanding tasks. Flat belt conveyors are often integrated into automated systems to handle tasks that could otherwise expose workers to hazardous environments or repetitive stress.
Reducing Exposure to Hazardous Environments
In certain industries, such as chemicals, pharmaceuticals, and food production, workers are often exposed to hazardous substances, high temperatures, or noisy environments. By incorporating flat belt conveyors into these systems, companies can automate the movement of materials, limiting workers’ exposure to these dangers. For example, in a chemical manufacturing plant, a flat belt conveyor can be used to transport raw materials or chemicals safely between different stages of production, reducing the need for manual handling in potentially dangerous conditions.
Decreasing Worker Fatigue and Stress
Repetitive tasks, especially in fast-paced environments, can lead to fatigue, which can negatively impact worker concentration and performance. Tasks like constantly moving products or materials from one place to another can quickly become monotonous, leading to mental and physical strain. Flat belt conveyors help alleviate this burden by taking over the task of moving materials, allowing workers to focus on other important activities. This reduction in repetitive tasks can help lower the risk of fatigue-related accidents, improving overall safety and productivity.
Handling Hazardous or Toxic Materials
Flat belt conveyors are an essential component in automated systems that handle hazardous or toxic materials, such as chemicals, pharmaceuticals, or biological substances. By using a conveyor to transport these materials, workers are kept at a safe distance from potential exposure, reducing the risk of chemical burns, inhalation of harmful fumes, or contamination. This not only improves safety but also complies with industry regulations regarding the safe handling and transportation of hazardous materials.
Enhanced Worker Visibility and Communication
Flat belt conveyors, when designed with transparency and proper integration into the workspace, help improve visibility and communication in the workplace, further enhancing safety.
Clear Line of Sight for Workers
Because flat belt conveyors typically offer a uniform and predictable design, workers can easily monitor the flow of materials on the system. This helps ensure that potential blockages or issues are quickly detected, preventing accidents from occurring due to misalignment or system malfunctions. When workers have a clear line of sight to the conveyor, they can respond promptly to any issues, improving both efficiency and safety.
Improved Communication Between Operators
In busy industrial settings, effective communication is key to maintaining a safe and efficient work environment. Flat belt conveyors are often designed to integrate seamlessly with other automated systems, allowing for better coordination between operators and machinery. When materials are moving automatically along a conveyor, operators can focus on monitoring the system, communicating effectively with other team members, and identifying problems early before they escalate.
Prevention of Overcrowding and Traffic
Conveyor systems like flat belt conveyors help organize the flow of materials, reducing the risk of congestion or overcrowding in work areas. When materials are consistently transported on a fixed path, there is less likelihood of workers needing to navigate crowded workspaces where they might be at risk of accidents or collisions. This organization also helps improve workflow efficiency, allowing workers to focus on their tasks with fewer distractions or obstacles.
Key Features to Consider When Choosing a Flat Belt Conveyor
When selecting a flat belt conveyor for your material handling needs, it’s essential to evaluate various factors that ensure the system meets your operational requirements. Flat belt conveyors are versatile and efficient, but not all conveyors are the same. The right choice depends on the specific demands of your industry, the materials you handle, and your workspace constraints. In this section, we’ll cover the key features to consider when choosing a flat belt conveyor to help you make an informed decision.
Belt Material and Design
The material of the flat belt and its design are crucial factors that directly affect the performance, durability, and suitability of the conveyor for your application.
Selecting the Right Material for Different Applications
Flat belt conveyors are made from a variety of materials, including PVC, rubber, polyurethane, and fabric-based belts. The material choice will depend on the types of products you are handling, the environment in which the conveyor operates, and the desired longevity. For instance:
PVC and Polyurethane: These materials are commonly used in food processing and packaging due to their non-toxic nature and ease of cleaning.
Rubber: Rubber belts are ideal for heavy-duty applications that involve transporting large or abrasive materials like metals, gravel, or construction materials.
Fabric-based belts: Fabric belts are lightweight and flexible, ideal for handling lightweight products, or in applications requiring more gentle handling.
Belt Surface and Texture
The surface of the belt can also vary. Flat belts can have smooth surfaces for easy product movement or textured surfaces (e.g., rough top or raised profiles) to provide better grip for certain products. For example, textured belts are useful for transporting inclined or slippery materials, preventing slippage during transit.
Modular vs. Continuous Belts
Some flat belt conveyors use modular belts, which consist of interlocking pieces that can be replaced individually if damaged, offering flexibility and ease of maintenance. Continuous belts, on the other hand, provide a seamless surface but might require more extensive repairs or replacements in the event of wear.
Load Capacity and Belt Speed
Two other critical factors to consider when selecting a flat belt conveyor are its load capacity and belt speed, both of which directly impact operational efficiency and effectiveness.
Choosing the Right Load Capacity for Your Operations
Load capacity refers to the maximum weight the conveyor belt can handle at any given time. Depending on your material handling needs, you must select a belt that can carry the appropriate load for your specific application:
Light-duty conveyors are suitable for small packages, bottles, or lightweight parts.
Heavy-duty conveyors are designed for large, bulky items like pallets or industrial machinery components.
Make sure to factor in the size and weight of the items you’re transporting. Undersized conveyors can lead to premature wear and potentially cause system breakdowns, while oversizing may lead to unnecessary energy consumption and higher initial costs.
Adjusting Belt Speed to Optimize Efficiency
The speed of the conveyor belt plays a major role in the efficiency of your operations. Flat belt conveyors come with adjustable speed settings, which are important for optimizing workflows:
Higher belt speeds may be needed for industries that require high throughput, such as e-commerce or assembly lines.
Lower speeds are ideal for delicate or precision tasks, like in food packaging or electronics assembly, where careful handling is essential.
Ensure that the belt speed is suitable for your production pace without compromising product quality or safety.
Customization and Adaptability
Flat belt conveyors are highly adaptable to meet the unique needs of different industries and production processes. Consider these customization options to tailor the system to your specific requirements.
Adjustable Frame and Belt Width
The ability to adjust the width of the conveyor belt allows for the accommodation of different product sizes. Some flat belt conveyors come with adjustable frames, enabling you to expand or reduce the width depending on the size of the materials being transported. This is especially useful in industries where the size and shape of products vary frequently, such as packaging or food processing.
Inclines and Angles
For industries that need to move materials between different elevation levels, choosing a conveyor system with adjustable incline and decline capabilities is essential. Many flat belt conveyors are designed to work at various angles, which makes them suitable for moving products from lower to higher levels or vice versa. Adjustable inclines help save space in tight facilities by allowing you to use vertical or inclined paths instead of taking up floor space with horizontal conveyors.
Custom Design Features for Specific Needs
Flat belt conveyors can also be tailored with features such as side guides, cleated belts, and sensors. Side guides can help ensure that materials stay centered on the belt, preventing misalignment. Cleated belts, which have raised sections, are particularly helpful when transporting items at an incline or when carrying products that are prone to rolling off. Additionally, incorporating sensors and automated controls can help with system integration, tracking, and monitoring, improving overall efficiency and control.
Environment and Temperature Resistance
The operating environment plays a significant role in determining the right type of flat belt conveyor for your needs, particularly when it comes to temperature, humidity, and exposure to chemicals or other harsh conditions.
Temperature Resistance
Some industrial environments expose conveyors to extreme temperatures, whether hot or cold. For example, conveyors used in food processing or electronics manufacturing may need to withstand temperatures that range from freezing to high heat. Materials like silicone or heat-resistant rubber are suitable for high-temperature applications, while belts made from polyester or polyurethane may work better in colder conditions.
Chemical Resistance
In industries like chemical manufacturing, pharmaceuticals, or waste management, flat belt conveyors might be exposed to corrosive substances. It’s essential to select a conveyor with a belt material that offers resistance to chemicals and abrasion, such as PVC or specialized rubber coatings, to ensure longevity and prevent degradation over time.
Water and Moisture Resistance
In environments with high humidity or exposure to liquids (such as in food processing or beverage industries), water resistance is another key consideration. Many flat belt conveyors are made with water-resistant materials or are treated with coatings that prevent moisture absorption. These features help prevent the belts from weakening, stretching, or losing their integrity when exposed to water or cleaning agents.
Ease of Maintenance and Durability
Finally, when choosing a flat belt conveyor, it’s essential to consider the long-term maintenance requirements and durability of the system. A good conveyor should be easy to maintain, service, and replace components if necessary.
Low Maintenance Requirements
A flat belt conveyor should be relatively easy to clean and maintain, especially in industries that require frequent sanitation (e.g., food processing). Some belts are designed with smooth surfaces that reduce the buildup of dirt or debris, while others may include features that allow for easier cleaning, such as removable components. Maintenance-friendly designs help reduce downtime and ensure the system operates efficiently over time.
Durability and Long Lifespan
The durability of the conveyor system is closely tied to the materials used and the construction quality. High-quality flat belt conveyors made from durable materials will last longer, even under heavy use. Consider the belt’s wear resistance, especially in applications where the conveyor handles abrasive materials or high-volume usage. Investing in a more durable system might involve a higher initial cost, but it can lead to lower overall maintenance and replacement costs in the long run.
Flat Belt Conveyors vs Other Conveyor Types: Why Flat Belts Stand Out
When it comes to material handling, choosing the right conveyor system is crucial for maximizing efficiency, safety, and cost-effectiveness. Among the different types of conveyor systems available, flat belt conveyors are one of the most popular and versatile options. However, they are often compared with other conveyor types, such as roller conveyors, screw conveyors, and chain conveyors, each of which offers unique advantages depending on the application.
In this section, we’ll explore the differences between flat belt conveyors and other common types of conveyors, highlighting why flat belts stand out in terms of performance, flexibility, and suitability for various industries.
Flat Belt Conveyors vs Roller Conveyors
Roller conveyors and flat belt conveyors are often compared due to their similar function of transporting materials along a fixed path. While they may seem like interchangeable options, there are some key differences that can make flat belt conveyors a better choice for certain applications.
Smooth and Continuous Surface
- Flat Belt Conveyors: One of the primary advantages of flat belt conveyors is the smooth, continuous surface they provide for material handling. This allows for the efficient and stable transportation of items, especially those that are fragile, small, or prone to shifting. The uniform surface helps prevent products from tipping, rolling, or falling, making it ideal for precise operations like electronics assembly or food processing.
- Roller Conveyors: In contrast, roller conveyors feature rotating cylindrical rollers, which can be ideal for heavier loads or items with a flat bottom. However, these conveyors can sometimes create issues when transporting smaller or irregularly shaped items, as they may slip or get stuck between rollers. This is especially true if the items are lightweight or have uneven surfaces, which can lead to misalignment and jamming.
Flexibility and Versatility
- Flat Belt Conveyors: Flat belts are highly flexible and can easily transport a variety of materials of different shapes and sizes. They can be used for both light and heavy-duty applications, such as small parts in an assembly line or large bulky items like packages in a warehouse. The ability to adjust the speed and direction of the belt also adds to its versatility.
- Roller Conveyors: While roller conveyors excel in handling heavy or large items (such as pallets or crates), they are less versatile when it comes to handling smaller, lighter materials or products with varying shapes. The fixed spacing between rollers can limit the types of items that can be conveyed efficiently. They are also not as adaptable for handling materials at different angles or inclines without additional modifications.
Noise and Vibration
- Flat Belt Conveyors: Flat belt conveyors tend to operate more quietly and with less vibration, making them ideal for environments that require a quieter work environment, such as laboratories or food production facilities. The smooth motion of the belt reduces noise levels, creating a more comfortable workplace.
- Roller Conveyors: Roller conveyors can be noisier, especially when moving large or heavy items, due to the metal-on-metal contact between the rollers and the materials being transported. This can be a drawback in applications where minimizing noise is a priority.
Flat Belt Conveyors vs Screw Conveyors
Screw conveyors and flat belt conveyors serve similar purposes in terms of moving materials, but they differ significantly in their design and capabilities. Screw conveyors are commonly used in industries where bulk materials such as grains, powders, or liquids need to be transported.
Material Handling
- Flat Belt Conveyors: Flat belt conveyors are ideal for handling a wide range of materials, including delicate, packaged products and bulkier items. They are versatile in the types of products they can carry, from light to heavy loads. The smooth surface of the flat belt ensures that materials remain stable and don’t spill or shift, making them perfect for industries that require precise, stable material movement.
- Screw Conveyors: Screw conveyors excel at transporting bulk materials like grains, powders, and liquids, particularly when the materials need to be moved horizontally or at a slight incline. The helical screw design pushes materials forward in a continuous manner, but this is not as suitable for products that need to remain undisturbed or for applications requiring a smooth, stable transport system.
Space Efficiency
- Flat Belt Conveyors: Flat belt conveyors are typically more space-efficient than screw conveyors, especially when the need for elevation changes arises. Flat belts can be configured to move materials in a straight line or around curves, making them adaptable to different layouts. They also handle varying belt widths and speeds with ease, optimizing the available space in a facility.
- Screw Conveyors: Screw conveyors are usually bulkier and require more space, particularly when handling large amounts of material. They may also need additional space for the auger and housing, making them less space-efficient compared to flat belt conveyors, especially when space is limited.
Maintenance and Cleanliness
- Flat Belt Conveyors: Flat belt conveyors are easier to clean and maintain compared to screw conveyors. The smooth surface and lack of internal moving parts make them easier to sanitize, especially important in industries like food processing, pharmaceuticals, or electronics. Regular maintenance, such as belt inspections and lubrication, is typically straightforward and involves minimal downtime.
- Screw Conveyors: Screw conveyors, on the other hand, are more prone to buildup and clogging, especially when handling granular or powdery materials. The internal auger design can make cleaning more difficult, as residue can accumulate around the screw mechanism. Additionally, the need for regular inspection of the auger’s integrity adds to the maintenance burden.
Flat Belt Conveyors vs Chain Conveyors
Chain conveyors are often used in heavy-duty industrial applications, particularly when handling large, heavy materials such as pallets, automotive parts, or large containers. However, flat belt conveyors have distinct advantages when compared to chain conveyors.
Load Handling
- Flat Belt Conveyors: Flat belt conveyors can handle a broad range of materials and weights. While they are typically used for lighter loads, flat belt conveyors can be adapted to handle heavier items with modifications such as stronger belts or added support structures. Additionally, they excel in handling materials of irregular shape or size, especially delicate items that need to be transported without damage.
- Chain Conveyors: Chain conveyors, by contrast, are designed specifically for heavy-duty applications and are better suited for transporting large, heavy loads. They are commonly found in industries such as automotive manufacturing, where they are used to move large components through production lines. However, chain conveyors are less suited for fragile items, as the rigid nature of the chain can cause damage to sensitive products.
Durability and Maintenance
- Flat Belt Conveyors: Flat belt conveyors generally require less maintenance compared to chain conveyors. With fewer moving parts and simpler mechanics, flat belt conveyors have a longer lifespan when properly maintained. They are easier to clean and repair, making them a more cost-effective option in the long run.
- Chain Conveyors: While chain conveyors are durable and built to withstand heavy loads, they require more maintenance due to their moving parts. Over time, the chains can wear out, stretch, or become misaligned, requiring regular inspection and lubrication to keep the system functioning efficiently. Additionally, chain conveyors are prone to noise and vibrations, which can affect the working environment.
Noise and Vibration
- Flat Belt Conveyors: As mentioned earlier, flat belt conveyors operate with minimal noise and vibration. This makes them ideal for workplaces that require a quieter environment, such as in food packaging, electronics, or pharmaceutical manufacturing.
- Chain Conveyors: Chain conveyors can be much noisier due to the clanking of the metal chain links and the rigid structure of the system. The noise can be disruptive, especially in environments where a quieter operation is preferred.