The hydraulic pump is the power component of the hydraulic system, which is driven by the engine or electric motor to suck oil from the hydraulic oil tank, form a pressure oil discharge, and send it to the actuator.
How does the hydraulic pump work?
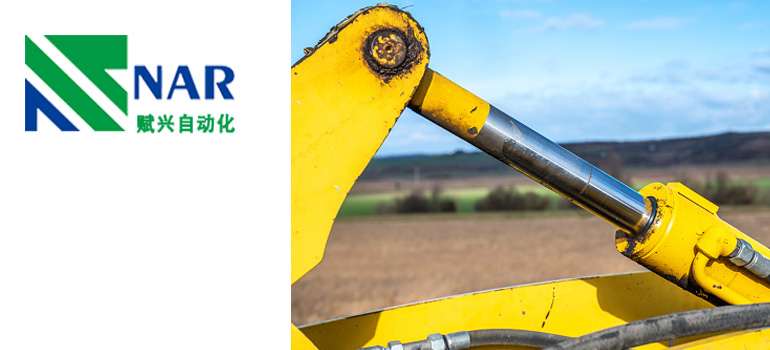
The hydraulic pump is the change of pump cavity volume caused by movement. The compressed fluid makes the fluid have pressure energy. The flow generated by it has enough power to overcome the pressure caused by the load.
The hydraulic pump performs two functions during operation. First, its mechanical action creates a vacuum at the pump inlet, and then allows the atmospheric pressure to force the liquid out of the reservoir, and then pumps it to the pump inlet pipeline. Secondly, its mechanical action will deliver this liquid to the pump outlet and force it into the hydraulic system.
There are many factors affecting the operation of hydraulic pump, such as its own design, selection of coupling, oil filter and other relevant accessories.
What are the most common types of hydraulic pumps?
Three common design types of hydraulic pump are vane pump, gear pump, and plunger pump. All of these are very suitable for ordinary hydraulic applications. If they can not meet the requirements of ordinary hydraulic systems, plunger pumps should be selected.
Most of the pumps used in the hydraulic system are positive displacement pumps. This means that they discharge (deliver) the same amount of liquid for each rotation cycle of the pump element. No matter how the pressure changes, the delivery volume of each cycle is almost unchanged.
According to whether the flow is adjustable, it can be divided into two types: variable displacement pump and constant displacement pump. The output flow that can be adjusted according to demand is called a variable displacement pump, and the flow that cannot be adjusted is called a constant displacement pump.
The quantitative pump has low noise, so it is very suitable for use in theatres, opera houses and other places. On the other hand, variable displacement pump is particularly suitable for circuits using hydraulic motors and circuits requiring variable speed or reverse capability.
Learn more about hydraulic vane pump
The vane pump uses the back-and-forth movement of the rectangular blade in the groove and the pump casing to press the suction liquid from the oil inlet side to the pump at the oil discharge side.
The vane pump has uniform flow, stable operation, and low noise. A vane pump can be divided into double-acting and single-acting-vane-pimps. The simplest vane pump consists of a circular rotor, which rotates in a large circular cavity. The centers of the two circles are offset, resulting in eccentricity. The blades slide in and out of the rotor and seal all edges. This will produce a blade chamber for pumping.
When the blades travel farther than the pump suction, a vacuum will be generated. This is how the oil is sucked into the pump chamber. The oil travels through the ports and is forced out of the pump discharge port. The direction of oil flow may change depending on the rotation of the pump. This is the case with many rotary pumps.
Where is the hydraulic vane pump used? The common applications of vane pumps are fuel loading terminals and fuel transport vehicles.
How does the hydraulic gear pump work?
Gear pump is one of the most common pump types in hydraulic fluid power applications.
The gear pump is a rotary pump that transports liquid or pressurizes it by changing and moving the working volume formed between the pump cylinder and the meshing gear. Two closed spaces are composed of two gears, the pump body, and the front and rear covers. When the gear rotates, the volume of the space on the gear disengaged side becomes small and large, forming a vacuum, and the liquid is sucked in. The volume of the space on the gear meshing side changes from large to small, and the liquid is squeezed into the pipeline. The suction cavity and the discharge cavity are separated by the meshing line of two gears. The pressure gear pump depends entirely on the resistance at the pump outlet.
It is easier to prevent catastrophic failure by using hydraulic gear pump. This is because the gear will gradually wear the housing and/or the main bushing. Therefore, gradually reduce the volumetric efficiency of the pump until it is almost useless. This usually occurs long before the equipment gets stuck or damaged due to wear.
Can the hydraulic gear pump reverse? Yes, most pumps can be reversed by disassembling the pump and turning the middle part. This is why most gear pumps are symmetrical.
What is the purpose of hydraulic gear pump?
The gear pump is characterized by simple and compact structure, small volume, large speed range and convenient maintenance. The petrochemical industry uses gear pumps to transport: diesel, asphalt, lubricating oil, crude oil and other fluids. The chemical industry also uses them for materials such as plastics, acids, sodium silicate, mixed chemicals and other media. Finally, these pumps are also used to transport: ink, paint, resin and adhesive, and food industry.
Learn more about plunger pump?
The plunger pump is an important device in the hydraulic system. It relies on the reciprocating movement of the plunger in the cylinder block to change the volume of the sealing working chamber to achieve oil absorption and pressure. The plunger pump has the advantages of high-rated pressure, compact structure, high efficiency, and convenient flow regulation.
Plunger pumps are widely used in high-pressure, large-flow and flow-regulating situations, such as hydraulic presses, construction machinery and ships.