Summary:
Mining Belt Conveyor Systems: Key Features and Innovations to Boost Productivity
Understanding the Core Components of Mining Belt Conveyors
How to Choose the Right Mining Belt Conveyor for Your Operation
Innovative Technologies Enhancing Mining Belt Conveyor Efficiency
Mining Belt Conveyor Systems: Safety Features and Best Practices
Challenges and Solutions in Mining Belt Conveyor Operations
Mining belt conveyors are the backbone of material handling in mining operations. These systems transport bulk materials—like ores, coal, and aggregates—over long distances, often in challenging environments. When it comes to maximizing efficiency and reducing operational costs, understanding the key features of these conveyors is crucial.
Understanding the Core Components of Mining Belt Conveyors
At the heart of any mining belt conveyor system are its core components, each of which plays a vital role in ensuring smooth and efficient operations. The most essential parts include the conveyor belt itself, pulleys, idlers, and the drive system.
- Conveyor Belt: The belt is the primary means of transportation, typically made from durable materials such as rubber, steel, or PVC. Its strength and flexibility are essential for handling heavy loads and withstanding harsh conditions.
- Pulleys and Rollers: Pulleys, located at both ends of the conveyor, help to drive and guide the belt, while rollers (or idlers) are used along the length of the conveyor to support the belt and reduce friction.
- Drive System: This consists of electric motors, gearboxes, and control systems that power the movement of the belt. The efficiency and reliability of the drive system are crucial for maintaining a consistent material flow.
By understanding how these components work together, mining operators can ensure the system operates smoothly, reducing downtime and improving overall productivity.
How to Choose the Right Mining Belt Conveyor for Your Operation
Selecting the ideal mining belt conveyor involves more than just picking a standard model off the shelf. Each mining operation is unique, and choosing the right conveyor requires careful consideration of factors such as material type, distance, and environmental conditions.
- Material Type: Different types of bulk materials have varying characteristics—some may be more abrasive or sticky than others, which affects the type of belt material and structure you’ll need. For example, coal and ore require different types of belts due to their specific handling requirements.
- Distance and Elevation: The longer the distance the conveyor needs to cover, the more important it becomes to choose a conveyor system that offers stability and minimal maintenance. Additionally, if the conveyor needs to move materials up or down steep inclines, certain belt designs (like steep-angle conveyors) are better suited for such tasks.
- Environmental Conditions: Extreme temperatures, humidity, and exposure to chemicals can significantly affect the lifespan and performance of mining belt conveyors. In these cases, specialized materials or coatings are often needed to ensure the system can operate under challenging conditions.
A well-chosen conveyor system not only improves efficiency but also reduces maintenance costs in the long run, making it a crucial investment for any mining operation.
Essential Maintenance Practices for Mining Belt Conveyors
To keep a mining belt conveyor running at peak performance, regular maintenance is necessary. This ensures that all components are functioning properly and minimizes the risk of costly breakdowns. Some key maintenance practices include:
- Regular Inspections: Inspecting the belt for signs of wear and tear is critical. Look for damage such as cuts, gouges, or fraying. Pulleys and rollers should also be checked to ensure they are aligned and turning smoothly.
- Cleaning and Lubrication: Dirt, debris, and build-up can cause friction and premature wear. Keeping the conveyor clean, especially around the rollers and pulleys, helps reduce wear and ensures smooth operation. Lubricating moving parts like the drive system also prevents excessive friction and heat buildup.
- Belt Tension Adjustment: Over time, the conveyor belt can lose tension, which can cause slippage or reduce its ability to carry material effectively. Periodic tension adjustments are important to maintain proper alignment and material flow.
Routine maintenance extends the life of the conveyor system, improves efficiency, and reduces the likelihood of unexpected downtime that can disrupt mining operations.
Innovative Technologies Enhancing Mining Belt Conveyor Efficiency
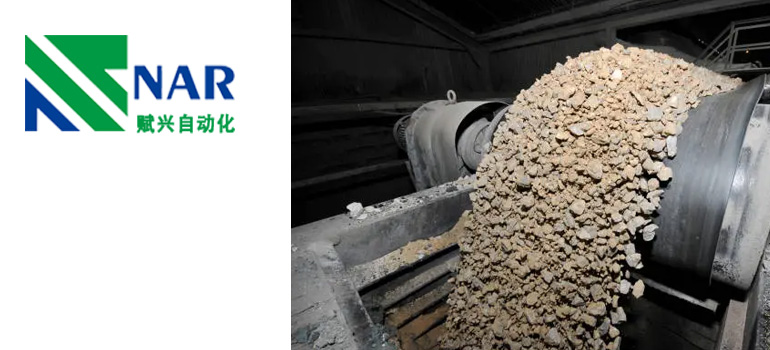
In today’s rapidly evolving mining industry, the efficiency of operations is more important than ever. Mining belt conveyors, which are essential for transporting materials across vast distances, are no exception. Thanks to innovations in technology, mining companies can now enhance the performance, safety, and overall productivity of their conveyor systems. From smart monitoring solutions to energy-saving features, these advancements are transforming the way we handle materials in mining operations.
The Role of IoT in Mining Belt Conveyor Monitoring
The Internet of Things (IoT) is revolutionizing the mining industry, particularly when it comes to improving the efficiency of mining belt conveyors. By integrating IoT-enabled sensors and devices into conveyor systems, mining operations can achieve real-time monitoring and predictive maintenance, which significantly reduces downtime and improves productivity.
- Real-Time Data Collection: IoT sensors embedded in key components (such as pulleys, motors, and belts) continuously collect performance data. This data can be accessed remotely via cloud platforms, allowing operators to monitor conveyor health from anywhere in the world.
- Predictive Maintenance: One of the biggest advantages of IoT is its ability to predict failures before they happen. By analyzing sensor data, machine learning algorithms can identify patterns that indicate potential issues, such as overheating motors or belt misalignment. This allows for proactive repairs, avoiding unplanned shutdowns and costly repairs.
- Optimized Performance: With IoT, operators can track various performance metrics in real-time—such as load, speed, and power consumption—allowing for more precise control over the conveyor system. This ensures that the system is running at peak efficiency, minimizing energy consumption and extending the life of the equipment.
By leveraging IoT, mining companies can significantly reduce maintenance costs and ensure their mining belt conveyors are operating smoothly, with minimal downtime.
Automation and AI in Mining Belt Conveyor Systems
Automation and artificial intelligence (AI) are increasingly being applied to mining belt conveyor systems to optimize operations and enhance efficiency. These technologies not only streamline processes but also improve safety and reduce human error.
- Automated Material Flow Control: AI systems can analyze incoming material characteristics (such as size, weight, and moisture content) and automatically adjust conveyor speeds and settings for optimal material flow. This reduces waste, ensures more consistent transport, and maximizes throughput.
- Autonomous Conveyor Operations: With automation, conveyors can be set to run with minimal human intervention. Sensors and AI-based control systems can adjust the speed of the conveyor based on the material being transported, its weight, and even environmental factors like weather or temperature changes. This flexibility helps maximize efficiency and ensures a smoother, more predictable operation.
- AI-Driven Diagnostics: AI is also being used to enhance diagnostics by continuously analyzing data from the conveyor system. AI-powered tools can predict component wear and tear and automatically order replacement parts before a failure occurs, reducing downtime and ensuring that the conveyor system stays operational.
Automation and AI are helping mining companies reduce the need for manual intervention, enhance system precision, and improve overall throughput and safety.
Energy-Efficient Innovations in Mining Belt Conveyors
Energy efficiency is a critical concern for mining operations, which often run 24/7. The energy costs associated with running large conveyor systems can be significant, but thanks to recent technological advancements, mining companies now have a range of options to reduce energy consumption and lower operational costs.
- Variable Frequency Drives (VFDs): One of the most significant energy-saving innovations in mining belt conveyors is the use of variable frequency drives. VFDs adjust the speed of the conveyor belt to match the material load, ensuring that the system is not using more energy than necessary. This results in a more efficient and cost-effective operation.
- Regenerative Drives: Regenerative drive systems convert excess energy generated by the conveyor’s braking process back into electrical energy, which can then be fed back into the power grid or used by other equipment on-site. This reduces the overall energy consumption of the system and can even make the operation partially self-sustaining.
- Energy-Efficient Conveyor Design: Advances in conveyor design, such as the use of lighter materials for belts and more efficient motors, have also contributed to energy savings. New belt materials, for example, are stronger and more durable, which reduces friction and energy loss. Additionally, improved motor technologies are able to deliver more power with less energy consumption.
These energy-efficient solutions not only reduce costs but also contribute to more sustainable mining practices, aligning with global efforts to reduce carbon footprints.
Mining Belt Conveyor Systems: Safety Features and Best Practices
Mining belt conveyors are integral to transporting materials in mining operations, but they also pose significant safety risks if not properly managed. As these systems are often running continuously and in challenging environments, ensuring the safety of workers and minimizing accidents is a top priority. By implementing robust safety features and following best practices, mining companies can create a safer working environment and enhance the overall efficiency of their conveyor systems.
Ensuring Safety with Guardrails and Emergency Stops
One of the fundamental safety features in any mining belt conveyor system is the installation of guardrails and emergency stops. These are crucial for preventing accidents, particularly around moving parts that are often unprotected or difficult to see.
Guardrails and Barriers: Guardrails around the conveyor belt, particularly in areas where workers are in close proximity, help prevent accidental falls or contact with moving parts. In high-risk zones, such as near the drive motor or rotating pulleys, adding additional barriers can protect workers from getting too close.
Emergency Stop Mechanisms: Emergency stop switches or pull-cords should be installed along the length of the conveyor. These devices allow operators to halt the system instantly in case of an emergency. It’s essential that these stop mechanisms are easy to reach, well-marked, and regularly tested to ensure they function correctly when needed.
The safety of operators can be significantly improved by these simple but effective safety features, reducing the likelihood of serious injuries.
Preventing Slips and Falls on Mining Belt Conveyors
Slips, trips, and falls are among the most common workplace accidents in mining environments, and conveyors are no exception. To mitigate this risk, several safety measures should be implemented:
Non-slip Surfaces: Conveyor walkways should be fitted with non-slip surfaces or grating to provide better traction, especially in wet or oily environments. This is particularly important for maintenance staff who often walk alongside or on top of conveyor belts to perform routine checks.
Proper Lighting: Adequate lighting in conveyor areas is crucial to ensure that workers can see clearly and avoid potential hazards. Poor lighting in maintenance areas or near conveyor drives can contribute to accidents, so lighting systems should be strategically placed along the length of the conveyor.
Training and Signage: Ensuring that all workers are trained in safe practices around conveyors can prevent many accidents. This includes understanding the importance of maintaining a safe distance from moving parts and knowing the proper way to access and inspect the equipment. In addition, clear signage indicating hazards or restricted areas is essential for maintaining safety on site.
The Importance of Regular Safety Inspections for Mining Belt Conveyors
Routine inspections and maintenance are essential for ensuring the safety of mining belt conveyor systems. Conveyor failures due to neglected maintenance can lead to dangerous situations, from belt slippage to equipment malfunction, posing risks to workers.
Visual Inspections: Conveyor systems should be inspected regularly to check for visible signs of wear, such as fraying belts, loose components, or any debris that may obstruct the flow of materials. Inspecting pulleys and rollers for damage or misalignment is also critical to prevent accidents.
Mechanical Inspections: Mechanical components like the drive motor, bearings, and conveyor belt tensioning devices should be checked periodically to ensure they are functioning properly. Worn-out or damaged components should be replaced promptly to avoid unexpected breakdowns that could lead to hazardous situations.
Safety Drills and Checks: Performing regular safety drills is another key component in maintaining a safe working environment. These drills should focus on emergency procedures, such as the proper use of emergency stop systems, and familiarize workers with the steps to take in the event of a conveyor malfunction.
Frequent inspections and preventive maintenance ensure that any safety concerns are identified and addressed before they become a serious issue, keeping workers and equipment safe.
Training and Best Practices for Conveyor Safety
Safety training plays a critical role in preventing accidents related to mining belt conveyors. Workers should be fully educated on the specific risks associated with conveyors and trained in safe operating practices.
Comprehensive Training Programs: Operators and maintenance staff should undergo thorough training that covers the safe use of mining belt conveyors, including how to properly load materials, how to adjust belt tension, and the correct procedures for stopping and starting the system. Training should also include awareness of emergency stop procedures and safety systems in place.
Safe Work Practices: Establishing a set of standard operating procedures (SOPs) for working around mining belt conveyors is essential. This includes safe methods for cleaning, inspecting, and maintaining conveyors, as well as protocols for troubleshooting and repair work. SOPs should be regularly updated to reflect any changes in technology or equipment.
Behavioral Safety Programs: Encouraging a safety culture within the workforce is just as important as physical safeguards. Behavioral safety programs, which promote the active participation of employees in maintaining a safe workplace, can help reduce unsafe behavior and foster a proactive approach to safety.
Implementing Automation to Enhance Conveyor Safety
In addition to physical safety features, automation is helping improve the overall safety of mining belt conveyor systems. Automated monitoring and control systems are becoming more common, offering additional layers of protection for workers.
Automated Shutoff Systems: Conveyor systems can be equipped with automated shutdown protocols that engage if a fault or unsafe condition is detected, such as unusual vibrations or overheating. These automated responses can prevent accidents before they escalate.
Remote Monitoring and Control: Some modern conveyor systems now feature remote monitoring capabilities, allowing operators to monitor system performance from a safe distance. This reduces the need for workers to physically interact with the conveyor during high-risk situations, such as when performing repairs or adjustments.
By integrating automation into safety protocols, mining companies can further reduce the likelihood of human error and improve the overall safety of their conveyor systems.
Challenges and Solutions in Mining Belt Conveyor Operations
Mining belt conveyors are vital for the smooth operation of material transport in mining environments. However, like any complex system, they come with their own set of challenges. From wear and tear to the harsh environmental conditions, mining belt conveyors face a variety of operational difficulties that can impact efficiency, safety, and cost-effectiveness. In this section, we’ll explore some of the most common challenges and offer practical solutions to overcome them.
Addressing Wear and Tear in Mining Belt Conveyors
One of the most common challenges faced by mining belt conveyors is the wear and tear of the belt and other critical components. Due to the heavy loads and abrasive materials being transported, the conveyor system experiences significant stress over time. The effects of this wear can lead to reduced system efficiency, higher maintenance costs, and even unexpected breakdowns.
Challenge: Conveyor belts can experience surface degradation, stretching, or cracking, leading to costly downtime and replacements. Pulley systems, idlers, and rollers also wear out due to constant friction and material load.
Solution: To address this, mining operators can invest in high-quality, durable materials for belts, pulleys, and rollers. For example, using belts made of rubber compounds with reinforced fabric can reduce abrasion and extend the lifespan of the system. Additionally, regular inspections and timely maintenance are key to identifying wear early and replacing parts before they fail. Implementing predictive maintenance powered by IoT sensors can also help detect signs of wear before they become critical, reducing unexpected repairs.
By selecting the right materials and focusing on preventative maintenance, mining companies can reduce downtime and extend the life of their conveyor systems.
Overcoming Material Handling Challenges in Harsh Mining Environments
Mining environments are often extreme, with high temperatures, dust, moisture, and corrosive materials. These harsh conditions place additional strain on mining belt conveyors, affecting both the performance of the system and the safety of the workers.
Challenge: Exposure to extreme weather conditions and abrasive materials can cause rapid deterioration of the conveyor belt, idlers, and other system components. Dust and moisture buildup on the belt can also cause material slippage, reducing the conveyor’s efficiency and increasing the risk of jams or system breakdowns.
Solution: To combat these environmental challenges, it’s important to choose environmentally resistant materials for conveyor components. For instance, belts designed to resist UV rays, extreme temperatures, and moisture are essential for long-term durability in tough conditions. Corrosion-resistant coatings can also be applied to pulleys, rollers, and other components to prevent rust and degradation.
Additionally, implementing dust suppression systems can help reduce the accumulation of dust and debris on the conveyor, which improves both efficiency and safety. Regularly cleaning the conveyor and maintaining the system’s integrity is also crucial for avoiding material buildup and operational disruptions.
Dealing with Conveyor Belt Slippage and Misalignment
Another major challenge in mining belt conveyor operations is belt slippage and misalignment. These issues can occur due to improper tension, wear, or misalignment of the conveyor components, leading to inefficiency and potential damage to the system.
Challenge: If the conveyor belt is not properly aligned, it can drift off track, causing misalignment of the pulleys, which in turn can lead to uneven material flow and increased wear on the belt. Belt slippage occurs when the belt cannot maintain the necessary tension to move materials effectively, which can cause it to lose traction, slip, or even stop moving entirely.
Solution: To prevent slippage and misalignment, it’s essential to regularly check and adjust belt tension to ensure it is set correctly. Conveyor systems should also be regularly realigned to maintain optimal operation, and components should be lubricated to minimize friction and wear. In some cases, installing training idlers can help guide the belt and prevent misalignment.
Moreover, using variable frequency drives (VFDs) can help ensure that the conveyor motor operates at the correct speed, matching the load requirements and preventing slippage due to power inconsistency.
Upgrading Old Mining Belt Conveyor Systems
Older mining belt conveyor systems, while still functional, can pose significant challenges in terms of efficiency, safety, and maintenance. As technology advances, these older systems may become obsolete, requiring expensive repairs and causing frequent downtime.
Challenge: Older systems often lack the advanced monitoring and control features available in modern conveyor systems, which can result in inefficiency, increased energy consumption, and higher maintenance costs. These systems are also less adaptable to changing operational needs or increasing material volumes.
Solution: A cost-effective solution to this challenge is upgrading the old system with modern components and technologies. For example, retrofitting existing systems with IoT sensors for real-time monitoring can improve maintenance practices and reduce the risk of unexpected failures. Installing energy-efficient motors or integrating variable frequency drives can reduce energy consumption, making the system more cost-effective. Additionally, upgrading to modular conveyor designs can improve system flexibility and allow for easier scaling to meet growing material handling demands.
Upgrading the system doesn’t always require a complete overhaul; sometimes, replacing specific components or adding modern technologies can significantly boost performance without the full cost of a new system.
Managing Conveyor System Downtime and Maintenance Costs
Minimizing downtime and reducing maintenance costs are ongoing challenges for mining belt conveyor operations. Unexpected breakdowns, inefficient repairs, and the need for frequent component replacements can disrupt production and increase operational costs.
Challenge: Conveyor systems that require frequent maintenance or repair can result in unplanned downtime, leading to lost productivity and significant costs. Furthermore, the complexity of some conveyor systems makes it difficult for maintenance teams to quickly diagnose issues, causing delays.
Solution: To manage downtime more effectively, companies should implement predictive maintenance strategies that rely on real-time data from IoT sensors. These sensors monitor critical components such as the belt, pulleys, and motors, providing insights into potential failures before they occur. By addressing issues early, operators can avoid costly emergency repairs and ensure that the conveyor system continues to run smoothly.
Moreover, creating a comprehensive maintenance schedule that includes regular inspections, belt adjustments, and part replacements can help reduce unscheduled downtime. Investing in training for maintenance staff and using diagnostic tools can also help speed up repairs and reduce operational interruptions.