Summary:
Maximizing Efficiency: The Role of Packaging Systems in Modern Industry
The Importance of Packaging Systems in Modern Industry
Maximizing Efficiency Through Innovative Packaging Systems
Key Components of Effective Packaging Systems
Overcoming Challenges in Implementing Packaging Systems
The Importance of Packaging Systems in Modern Industry
In today’s rapidly evolving industrial landscape, packaging system stand as unsung heroes, quietly driving efficiency, sustainability, and profitability across a myriad of sectors. But what exactly makes these systems so indispensable in the modern industrial ecosystem?
Understanding the Vital Role of Packaging Systems
Packaging system serve as the linchpin of modern industry, orchestrating the seamless transition of products from production lines to consumers’ hands. These systems are not merely about enclosing goods in boxes or containers; they are meticulously designed and engineered to fulfill a multitude of critical functions and objectives.
Evolution of Packaging Systems in Industry
From humble beginnings as basic wrapping and containment solutions, packaging systems have undergone a remarkable evolution over the years. Today, they encompass a sophisticated array of technologies, materials, and processes, tailored to meet the diverse needs and demands of global supply chains.
Key Functions and Objectives of Packaging Systems
At their core, packaging systems are tasked with safeguarding products, preserving their integrity, and ensuring their safe arrival at their destination. However, their role extends far beyond mere protection. They also play a pivotal role in branding, marketing, and consumer engagement, serving as the frontline ambassadors of a company’s identity and values.
Impact of Packaging Systems on Efficiency and Productivity
Efficiency lies at the heart of every successful enterprise, and packaging systems are instrumental in driving operational efficiency and productivity. By streamlining processes, minimizing waste, and optimizing resource utilization, these systems help businesses stay competitive in today’s fast-paced marketplace.
In essence, packaging systems are the unsung heroes of modern industry, quietly but decisively shaping the way products are manufactured, distributed, and consumed. Their importance cannot be overstated, as they represent the nexus where innovation, efficiency, and consumer satisfaction converge.
Maximizing Efficiency Through Innovative Packaging Systems
Maximizing efficiency through innovative packaging systems is a cornerstone of modern industrial operations, where every aspect of production is meticulously optimized to enhance productivity and reduce waste. Let’s delve into how these innovative packaging systems revolutionize efficiency:
Innovations Driving Efficiency in Packaging Systems
Innovation is at the heart of progress, and packaging systems are no exception. From automated processes to sustainable materials, the latest advancements are transforming the way goods are packaged, shipped, and delivered.
Automation and Robotics: Transforming Packaging Processes
Automation and robotics have revolutionized packaging operations, streamlining processes, reducing labor costs, and increasing throughput. From robotic arms that pick and place products with precision to automated packaging lines that operate seamlessly around the clock, these technologies are driving unprecedented levels of efficiency in modern packaging systems.
Sustainable Packaging Solutions: Balancing Efficiency and Environmental Responsibility
In an era of heightened environmental awareness, sustainable packaging solutions are gaining traction as a key driver of efficiency. From biodegradable materials to minimalist designs that reduce waste, these innovations not only minimize environmental impact but also optimize resource utilization and reduce costs throughout the packaging lifecycle.
Smart Packaging Technologies: Leveraging Data for Optimization
The advent of smart packaging technologies has ushered in a new era of data-driven optimization. Embedded sensors, RFID tags, and IoT-enabled devices provide real-time insights into packaging performance, supply chain visibility, and consumer behavior. By harnessing this wealth of data, companies can identify inefficiencies, anticipate demand, and optimize packaging processes with unprecedented precision.
Case Studies: Success Stories of Efficiency Gains with Advanced Packaging Systems
Real-world examples speak volumes about the transformative power of innovative packaging systems. Case studies highlighting efficiency gains, cost savings, and competitive advantages achieved through the adoption of cutting-edge packaging technologies serve as compelling proof of concept, inspiring further innovation and investment in this critical area.
In summary, innovative packaging systems are not just about containing products—they’re about maximizing efficiency, minimizing waste, and delivering value at every step of the supply chain. By embracing automation, sustainability, and smart technologies, companies can unlock new levels of efficiency and competitiveness in today’s dynamic marketplace.
Key Components of Effective Packaging Systems
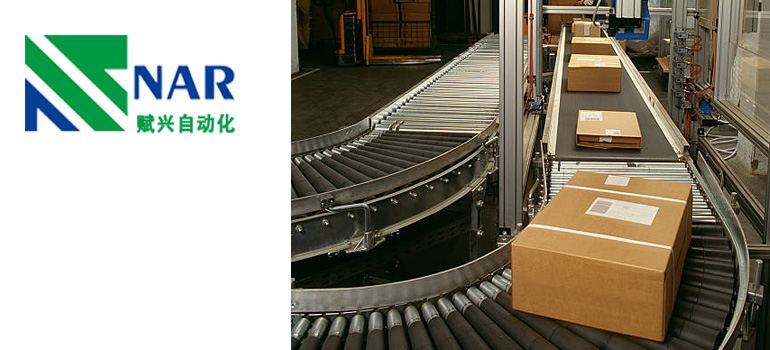
Effective packaging systems rely on a combination of key components to ensure optimal performance, reliability, and efficiency. Let’s explore these essential components in detail:
Designing Packaging Systems for Efficiency and Flexibility
Design is the foundation of any effective packaging system. It involves careful consideration of factors such as product specifications, packaging materials, transportation requirements, and end-user preferences. By designing packaging systems for flexibility and adaptability, companies can accommodate a wide range of products and packaging formats, streamline operations, and respond quickly to changing market demands.
Integration with Production Processes: Ensuring Seamless Operations
Seamless integration with production processes is essential for maximizing efficiency and minimizing downtime in packaging operations. Packaging systems should be seamlessly synchronized with upstream and downstream processes, allowing for smooth material flow, efficient handling, and minimal bottlenecks. This integration enhances overall operational efficiency and enables companies to meet production targets with precision and reliability.
Balancing Standardization and Customization in Packaging Solutions
Balancing standardization and customization is key to optimizing packaging systems for efficiency. While standardized packaging solutions offer economies of scale and simplified operations, customization allows companies to tailor packaging to specific product requirements, branding considerations, and customer preferences. By striking the right balance between standardization and customization, companies can optimize packaging efficiency without sacrificing flexibility or product differentiation.
Maintenance and Optimization Strategies for Packaging Systems
Effective maintenance and optimization strategies are essential for ensuring the long-term performance and reliability of packaging systems. Preventive maintenance practices, such as regular inspections, lubrication, and replacement of worn components, help minimize downtime and prolong equipment lifespan. Continuous improvement initiatives, such as process optimization, automation upgrades, and technology investments, enable companies to stay ahead of evolving market trends and maintain a competitive edge in packaging operations.
Utilizing Data Analytics to Identify and Address Efficiency Gaps
Data analytics play a crucial role in identifying and addressing efficiency gaps in packaging systems. By collecting and analyzing data from various sources, such as production metrics, equipment sensors, and customer feedback, companies can gain valuable insights into packaging performance, identify areas for improvement, and implement targeted optimization strategies. Whether it’s reducing packaging waste, improving throughput, or enhancing product quality, data-driven decision-making enables companies to achieve greater efficiency and competitiveness in packaging operations.
In summary, effective packaging systems rely on a combination of design, integration, customization, maintenance, and data-driven optimization to maximize efficiency and performance. By focusing on these key components, companies can build packaging systems that deliver value, reliability, and sustainability throughout the supply chain.
Overcoming Challenges in Implementing Packaging Systems
Overcoming challenges in implementing packaging systems requires careful planning, collaboration, and strategic problem-solving. Let’s delve into some common obstacles and effective strategies for addressing them:
Addressing Common Obstacles in Packaging System Integration
Implementing packaging systems can pose several challenges, including:
Cost Considerations and ROI Analysis for Packaging Investments: One of the primary challenges in implementing packaging systems is the initial cost outlay and the need to justify investments through return on investment (ROI) analysis. Companies must carefully evaluate the costs and benefits of implementing new packaging systems, considering factors such as equipment purchase costs, installation expenses, training, and potential savings in labor, materials, and operational efficiency.
Overcoming Resistance to Change: Strategies for Employee Buy-in: Resistance to change among employees can hinder the successful implementation of new packaging systems. To overcome this challenge, companies should prioritize effective communication, employee engagement, and training programs. By involving employees in the decision-making process, addressing concerns, and providing adequate training and support, companies can foster buy-in and facilitate smoother transitions to new packaging systems.
Regulatory Compliance and Quality Assurance in Packaging Systems: Regulatory compliance and quality assurance requirements pose significant challenges for companies implementing packaging systems, particularly in highly regulated industries such as pharmaceuticals and food processing. Companies must ensure that packaging systems meet regulatory standards for safety, quality, and traceability, while also maintaining operational efficiency and cost-effectiveness.
Best Practices for Successful Implementation of Packaging Systems
To overcome these challenges, companies can adopt the following best practices:
Stakeholder Collaboration and Cross-functional Teams: Keys to Success: Successful implementation of packaging systems requires collaboration and coordination among stakeholders from various departments, including operations, engineering, procurement, quality assurance, and regulatory compliance. By forming cross-functional teams and involving key stakeholders in the decision-making process, companies can ensure that packaging systems meet the needs and requirements of all stakeholders and align with broader business objectives.
Pilot Testing and Iterative Implementation: Minimizing Disruption and Maximizing Results: Pilot testing is an essential step in the implementation of new packaging systems, allowing companies to evaluate system performance, identify potential issues, and make necessary adjustments before full-scale deployment. By conducting pilot tests in controlled environments and gradually scaling up implementation based on feedback and results, companies can minimize disruption to operations and maximize the effectiveness of packaging systems.
Training and Skill Development: Empowering Employees for Success: Comprehensive training and skill development programs are essential for ensuring that employees are equipped to operate and maintain new packaging systems effectively. By providing hands-on training, workshops, and resources, companies can empower employees with the knowledge and skills they need to succeed in the new operating environment.
In summary, overcoming challenges in implementing packaging systems requires a proactive approach, collaboration among stakeholders, and adherence to best practices. By addressing cost considerations, fostering employee buy-in, ensuring regulatory compliance, and following best practices for implementation, companies can successfully implement packaging system that enhance efficiency, quality, and competitiveness.