Summary:
Belt Conveyor System vs. Roller Conveyors: Which is Best for Your Needs?
What is a Belt Conveyor System?
Advantages of a Belt Conveyor System
When to Choose a Roller Conveyor System?
Factors to Consider When Choosing Between Belt Conveyor and Roller Conveyors
Maintenance and Longevity: Belt Conveyor System vs. Roller Conveyors
When discussing material handling and transport systems, Belt Conveyor Systems and Roller Conveyors are two of the most common solutions. Each system has its unique features and advantages, making them suitable for different industries and needs. Understanding their principles and applications will help you make a more informed decision when choosing the right system.
What is a Belt Conveyor System?
A Belt Conveyor System, as the name suggests, relies on a continuous loop of a conveyor belt (often made of rubber, fabric, or plastic) to transport goods. The system works on a simple yet effective principle: powered rollers or drive units move the conveyor belt, which in turn carries items forward through frictional force. Belt conveyors are commonly used to move bulk materials, packaged goods, and even food products or small components.
Compared to other conveyor types, Belt Conveyor Systems offer great advantages in terms of carrying capacity and adaptability to various transport needs. Whether it’s horizontal, inclined, or declined transportation, a Belt Conveyor can efficiently handle it. They are especially well-suited for long-distance transportation or when handling lighter items.
How Do Roller Conveyors Work?
Unlike Belt Conveyor Systems, Roller Conveyors move items using a series of rollers. These rollers are usually placed within a framework, and they are powered by a drive system. Items move through the rollers by rolling along the surface, relying on their own weight to push them forward. In cases where the items are light, an external power source might be necessary to move them.
Roller Conveyors are ideal for applications where precise item placement is required, such as in automated warehouses or assembly lines. In some applications, roller conveyors can offer higher speed and more precise control compared to belt conveyors, especially for short-distance transport. Additionally, due to their simpler structure, roller conveyors tend to be more durable and require less maintenance, often translating into lower costs over time.
Key Differences Between Belt Conveyor Systems and Roller Conveyors
While both Belt Conveyor Systems and Roller Conveyors serve the purpose of material transport, there are some key differences in their design, application, and performance. Firstly, a Belt Conveyor can handle larger and heavier items, and is more adaptable for irregularly shaped products. In contrast, Roller Conveyors are usually suited for standardized products, such as boxes or other regularly shaped objects.
Secondly, Belt Conveyor Systems excel in transporting items on inclines and over long distances. Roller Conveyors, on the other hand, perform more efficiently in horizontal transportation and are particularly effective in high-speed and precise control applications. Lastly, Belt Conveyor Systems tend to require more maintenance, as the conveyor belts need regular checks and replacement, whereas Roller Conveyors are simpler and generally require less upkeep.
Advantages of a Belt Conveyor System?
Belt Conveyor Systems are a fundamental part of modern material handling and logistics, offering several advantages that make them an ideal choice for a wide range of industries. Whether it’s in manufacturing, mining, or distribution, the benefits of using a Belt Conveyor System are clear. Here are some of the key advantages:
Flexibility in Transportation of Materials
One of the standout features of a Belt Conveyor System is its flexibility. These systems can transport a wide variety of materials, from loose bulk items like sand and coal to packaged goods and heavy machinery. The design of the belt allows for easy adaptation to different environments, whether it’s moving items on a flat surface, inclined, or in curves. This adaptability is a major advantage in industries that handle diverse products with varying shapes and sizes.
Additionally, the belts can be customized with different materials such as rubber, PVC, or fabric, depending on the type of material being transported. This versatility makes it an excellent choice for a wide array of applications, from food processing to warehouse logistics.
Cost-Effectiveness of Belt Conveyor Systems
Belt Conveyor Systems are known for their relatively low operational costs. Once installed, they require minimal labor and can run for long periods with little intervention. The system can be automated, reducing the need for manual labor, which helps businesses cut down on staffing costs.
Compared to other transport systems, such as pneumatic or hydraulic conveyors, the cost of a Belt Conveyor System is often lower, both in terms of installation and maintenance. Additionally, their long lifespan and durability mean that businesses don’t have to worry about frequent replacements or repairs, making them a cost-effective long-term solution.
Ability to Handle Large Quantities of Material
Belt Conveyor Systems excel at transporting large quantities of material at a consistent rate. This is especially important for industries like mining, agriculture, and manufacturing, where high-volume movement of materials is essential. The continuous nature of the system means that materials can be moved quickly and efficiently without stopping, reducing delays and boosting overall productivity.
The capacity of a Belt Conveyor is largely dependent on the design of the system, and with the right configuration, it can handle large volumes of goods over extended distances. This makes it an ideal choice for businesses that need to transport large amounts of materials quickly and efficiently.
Maintenance Requirements for Belt Conveyor Systems
While every mechanical system requires some level of maintenance, Belt Conveyor Systems are relatively easy to maintain compared to other types of conveyors. The key components of the system, such as the belts, rollers, and pulleys, are designed to be robust and durable, ensuring the system operates smoothly for extended periods.
Routine maintenance often involves simple tasks, like checking the belt tension, cleaning the conveyor, and ensuring the system is properly lubricated. As long as these tasks are performed regularly, the system can continue running efficiently with minimal downtime. This ease of maintenance makes it a preferred choice for many businesses looking to streamline their operations.
Environmentally Friendly Solution
In today’s world, many companies are focusing on reducing their environmental impact. Belt Conveyor Systems offer an eco-friendly solution, especially when compared to alternatives like trucks or other fossil fuel-based transport methods. By utilizing electric motors and running continuously, Belt Conveyors reduce the need for vehicles, which not only lowers fuel consumption but also minimizes carbon emissions.
Additionally, Belt Conveyor Systems can be designed to include energy-efficient features, such as regenerative drives that convert kinetic energy into electricity, further contributing to sustainability efforts.
When to Choose a Roller Conveyor System?
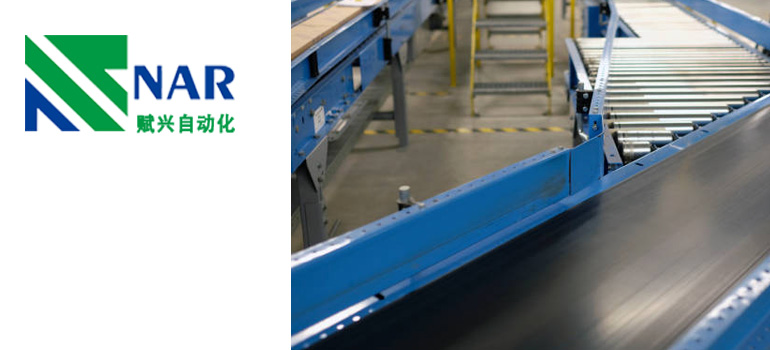
Roller Conveyor Systems are a highly efficient and versatile solution for material handling in various industries. However, like any other conveyor system, they are most effective in specific situations. Choosing a Roller Conveyor over a Belt Conveyor System depends on several factors related to your operational needs, material types, and overall production environment. Here are some scenarios where a Roller Conveyor System might be the best choice:
Ideal Applications for Roller Conveyors
Roller conveyors are typically best suited for environments where items need to be moved in a controlled, precise, and efficient manner. They are particularly effective in:
- Packaging and Sorting: Roller conveyors are widely used in sorting and packaging lines, where products are moved along a predetermined path for inspection, labeling, or packing. The precision with which items are transferred from one station to the next makes roller conveyors ideal for this purpose.
- Warehouse and Distribution Centers: In settings where products are consistently handled in bulk or stacked items are regularly moved, roller conveyors help ensure the smooth and efficient movement of items through storage areas. With gravity-driven roller systems, items can be moved effortlessly without the need for power.
- Assembly Lines: For applications where items are assembled or worked on at different stations, roller conveyors provide an easy solution to transport parts between workstations, enabling a continuous flow of goods. Their adaptability to various product sizes and their ability to handle multiple products simultaneously make them great for assembly processes.
Benefits of Roller Conveyors in Certain Environments
Roller conveyors are particularly useful when the following conditions apply:
Flat or Slightly Inclined Transport: Unlike Belt Conveyor Systems, which can transport items up inclines or declines, roller conveyors are more effective on level or slightly inclined surfaces. This is especially true when items are relatively light and can be pushed or moved using gravity. For instance, roller conveyors are commonly used in warehouse aisles, where materials move down simple inclined lanes.
Handling Heavy, Rigid, or Uniformly Shaped Items: Roller conveyors excel at transporting products with a consistent shape and weight, such as boxes, crates, and pallets. Since the system relies on the rolling motion of the items over the rollers, it is best for items that are rigid and relatively uniform. Products like barrels or bulk materials might not be ideal, as the rollers may not provide adequate support.
High-Speed Transport and Sorting: If speed is a critical factor in your material handling system, roller conveyors can offer faster processing than some other types of conveyors. Their ability to move large quantities of goods at high speeds makes them particularly well-suited for industries that need to handle high-volume, time-sensitive items, like e-commerce fulfillment or parcel sorting.
Cost Comparison: Belt Conveyor System vs. Roller Conveyors
When evaluating whether to choose a Roller Conveyor System, it’s essential to consider the cost in relation to its performance and suitability for your needs:
Lower Initial Investment: Roller Conveyor Systems generally come with a lower upfront cost compared to Belt Conveyor Systems, especially in applications where you don’t need the flexibility of an inclined or curved path. The simplicity of their design and fewer moving parts help keep costs down.
Reduced Energy Costs: Roller conveyors often require less energy to operate, especially when using gravity-driven roller conveyors. This makes them a more energy-efficient option in some cases, especially if the system relies on gravity to move goods, thus reducing the need for external power sources.
Maintenance and Repairs: Roller conveyors are generally easier and less costly to maintain than Belt Conveyor Systems. Their simple design with fewer moving parts means there’s less to break down. This can be a major cost-saving factor in industries where continuous, low-maintenance operation is essential.
When Precision and Control are Important
If your operation requires a high level of precision and control over how products move from one location to another, roller conveyors can be a great solution. Their ability to precisely position items at each station, such as in packaging, sorting, or assembly operations, ensures that goods are transferred accurately without risk of damage or misplacement. This precision is especially useful in automated environments where items need to be moved in a specific sequence or orientation.
How to Decide Which Conveyor System is Best for Your Needs
Choosing the right conveyor system is crucial for optimizing your material handling processes. Whether you’re selecting between a Belt Conveyor System or a Roller Conveyor System, several factors must be taken into account to ensure that the system you choose aligns with your specific operational requirements. Here’s a step-by-step guide on how to decide which conveyor system is the best fit for your business needs:
Factors to Consider When Choosing Between Belt Conveyor and Roller Conveyors
Type and Size of Material
Belt Conveyor Systems: If you’re transporting materials with irregular shapes or sizes, or if the material is light and needs to be supported along the entire transport path (like bulk items, food products, or small parts), a Belt Conveyor System is often the better choice. Belt conveyors can handle a wide range of materials and offer more flexibility, especially when transporting materials that need to be held securely in place on a surface.
Roller Conveyors: Roller conveyors are ideal for transporting rigid, uniform, or standardized items such as boxes, pallets, crates, and other items with a consistent size. If your materials are not bulky and their weight can be handled by gravity or external power, roller conveyors provide a simpler and more cost-effective solution.
Transporting Distance and Direction
Belt Conveyor Systems: Belt conveyors excel at long-distance transport, especially when the items need to be moved over uneven terrain or inclined surfaces. If your application requires moving materials across long distances or through complex, winding paths, belt conveyors are the more suitable option.
Roller Conveyors: Roller conveyors are more efficient in short-distance, horizontal applications where items need to be moved in a straight line or on a slight incline. They are typically used in areas where goods need to be moved between workstations or through packaging lines.
Speed and Throughput Requirements
Belt Conveyor Systems: If your operation requires steady, continuous movement of large quantities of goods, particularly if the goods are relatively lightweight or bulk, a Belt Conveyor System is the better choice. They can be optimized for higher throughput, especially in industries like manufacturing or mining, where heavy and bulk materials need to be continuously transported.
Roller Conveyors: Roller conveyors are great for high-speed operations, especially in sorting, packaging, and distribution environments where precise control over the flow of goods is necessary. Roller conveyors are ideal for environments where high-speed, efficient sorting is a priority, such as e-commerce or parcel shipping centers.
Environmental and Operational Conditions
Belt Conveyor Systems: Belt conveyors can be more adaptable to extreme environments, such as dusty or wet conditions, and can also handle elevated temperatures. In industries such as mining, food processing, or pharmaceuticals, a Belt Conveyor System can be fitted with materials designed to withstand specific environmental conditions.
Roller Conveyors: Roller conveyors, on the other hand, are more suited for indoor applications where environmental factors are controlled. If your operation involves handling lightweight goods in an environment where temperature, humidity, and dust are well-regulated, roller conveyors may provide a simpler, lower-maintenance solution.
Customizing Conveyor Systems for Specific Business Needs
When choosing a conveyor system, it’s important to customize it to fit the unique needs of your business. This could involve:
- Adjusting the Conveyor Speed: Some conveyors can be fitted with adjustable speed controls to match the pace of your production or handling needs.
- Designing Curved or Inclined Paths: If your layout involves moving products up, down, or around corners, you can design conveyor systems that integrate curves or inclined sections.
- Integrating Automation and Sensors: Both Belt and Roller Conveyor Systems can be equipped with sensors, automatic sorting features, and even robotic arms to increase automation. This helps improve efficiency in highly automated operations like assembly lines or warehouses.
Cost Considerations
Initial Investment
Belt Conveyor Systems: While Belt Conveyor Systems tend to have a higher upfront cost, especially if they involve complex features like adjustable inclines or heavy-duty belts, they are often the better choice when long-term durability and flexibility are essential.
Roller Conveyors: Roller conveyors typically have a lower initial cost, especially for applications that don’t require complex features or the movement of heavy, irregular materials.
Maintenance and Longevity
Belt Conveyor Systems: Belt conveyors tend to require more frequent maintenance than roller conveyors, mainly due to the wear and tear on the belt. Belts may need to be replaced over time, and regular checks are needed to ensure proper tension and alignment. However, with proper care, Belt Conveyor Systems can last a long time and offer excellent ROI in high-demand environments.
Roller Conveyors: Roller conveyors are generally low-maintenance, especially in gravity-driven designs, as they have fewer moving parts and require less upkeep. If you’re looking for a cost-effective solution with minimal ongoing maintenance costs, roller conveyors may be the more economical choice in the long run.
Expert Recommendations for Choosing the Right Conveyor System
Consult with Conveyor Experts: If you’re uncertain about which system will best suit your needs, it’s advisable to consult with industry experts or conveyor system manufacturers. They can perform an analysis of your operational requirements, provide detailed specifications, and offer recommendations on the best system for your needs.
Consider Future Growth: While short-term costs and needs are important, it’s also essential to consider future scalability. Choose a conveyor system that can grow with your business, whether that means adding more capacity, integrating with new technologies, or adapting to changing material types.
Maintenance and Longevity: Belt Conveyor System vs. Roller Conveyors
When choosing between a Belt Conveyor System and a Roller Conveyor, understanding the differences in maintenance requirements and system longevity is crucial to making an informed decision. Both systems have their own strengths and weaknesses in terms of upkeep and lifespan, and the best choice for your business will depend on your operational needs, budget, and environment. Let’s compare the maintenance and longevity of both conveyor systems.
Maintenance Challenges for Belt Conveyor Systems
Belt Conveyor Systems are typically more complex, which means they require more frequent and detailed maintenance. Some of the maintenance aspects that need to be managed include:
Belt Wear and Tear:
The most common maintenance issue for Belt Conveyor Systems is wear on the belt itself. Over time, belts can become frayed, torn, or stretched, especially in high-use environments. This means they need to be regularly inspected and replaced, which can result in significant downtime and labor costs if not proactively managed.
Preventive Maintenance: Regular checks are necessary to identify signs of wear, such as uneven tension, damaged belt surfaces, or misalignment. Using high-quality belts and implementing belt cleaning systems can help extend the life of the belt.
Roller and Pulley Maintenance:
Belt Conveyor Systems rely on rollers and pulleys to move the belt and keep it in place. These components can wear out over time due to friction, especially if the system handles heavy loads or abrasive materials. Routine lubrication and inspection of rollers and pulleys are essential to ensure smooth operation.
Belt Alignment: Misalignment can be a common issue, leading to uneven wear or damage to the belt. Ensuring that the system is properly aligned is a critical maintenance task.
Drive and Tensioning Mechanisms:
The motor, drive unit, and tensioning mechanisms on a Belt Conveyor System require periodic checks to ensure that they are functioning properly. The drive motor can overheat if it’s not adequately maintained, leading to failure.
Belt Tensioning: Improper belt tension can cause excessive wear and reduce the system’s efficiency. Regular tensioning adjustments and checks are necessary.
Longevity of Belt Conveyor Systems:
With proper maintenance, Belt Conveyor Systems can last for many years, sometimes even decades, depending on the environment and the quality of components used. However, due to the regular need to replace belts, pulleys, and other components, the overall cost of ownership can be higher over time compared to roller conveyors.
Roller Conveyor System Durability and Maintenance Needs
In contrast to Belt Conveyor Systems, Roller Conveyors are generally simpler in design and require less maintenance overall. However, there are still some maintenance aspects to consider:
Roller Wear:
Roller Conveyors rely on the rollers to move goods along the system. Over time, the rollers can wear down, especially if they’re handling heavy or abrasive materials. The rollers may also become misaligned or clogged, particularly in dusty or dirty environments. Regular cleaning and lubrication can help prevent wear and reduce the risk of damage.
Maintenance: Rollers need to be inspected periodically for signs of wear or obstruction. They should be cleaned regularly, especially in environments where dust, dirt, or other particles are present. In some cases, individual rollers can be replaced without impacting the entire system.
Minimal Moving Parts:
One of the major benefits of Roller Conveyors is that they have fewer moving parts than Belt Conveyor Systems, which means there is less potential for mechanical failure. This results in lower maintenance requirements and fewer breakdowns, making them easier and cheaper to maintain.
Gravity vs. Powered Rollers: Gravity roller conveyors (where items are moved without power) typically require less maintenance than powered roller conveyors, which use motors to drive the rollers. In powered systems, the motor and drive components need periodic attention.
No Belt Replacement:
A significant maintenance advantage of Roller Conveyors over Belt Conveyor Systems is the absence of a conveyor belt that wears out. Since the rollers themselves are designed to last longer and can be replaced individually, Roller Conveyors tend to have lower long-term maintenance costs. There is no need to replace belts regularly, which can result in fewer disruptions and reduced downtime.
Lubrication and Alignment:
The rollers need to be properly lubricated to prevent friction and ensure smooth operation. This task is relatively simple but needs to be performed periodically. Additionally, misalignment of rollers can cause uneven transport, so regular checks are necessary to ensure that all rollers are functioning properly.
Longevity of Roller Conveyors:
Roller Conveyor Systems typically have a longer lifespan due to their simpler design and fewer moving parts. With proper maintenance, roller conveyors can operate for several decades. Since rollers are often replaceable individually, they can be maintained and repaired in parts rather than replacing the entire system, which further reduces costs over time.