Summary:
Choosing the Right Mobile Vessel Loader for Your Port Operations: Key Considerations
Understanding the Types of Mobile Vessel Loaders
Key Features to Look for in a Mobile Vessel Loader
Cost Factors and Budgeting for a Mobile Vessel Loader
Assessing the Supplier and Support Services
Understanding the Types of Mobile Vessel Loaders
When selecting a mobile vessel loader for your port operations, it’s crucial to understand the different types available and how they fit your specific needs. Mobile vessel loaders come in various designs and configurations, each offering distinct advantages and features. Here’s a closer look at the main types:
Different Types of Mobile Vessel Loaders
Hydraulic Mobile Vessel Loaders: Hydraulic loaders are known for their powerful lifting capabilities and versatility. They use hydraulic systems to operate the boom and other components, providing smooth and efficient movement. These loaders are particularly effective for handling heavy and bulk cargoes, making them a popular choice for ports with high-volume operations. Their strength and adaptability make them suitable for various vessel sizes and types.
Electric Mobile Vessel Loaders: Electric loaders are an environmentally friendly option that uses electric power to operate. They are quieter and produce fewer emissions compared to their diesel counterparts, which can be advantageous in ports with stringent environmental regulations. Electric loaders are ideal for operations where noise and air quality are a concern. They are also often more energy-efficient and can reduce long-term operating costs. However, they may require access to a reliable power source and may have limitations in terms of lifting capacity compared to hydraulic models.
Hybrid Mobile Vessel Loaders: Hybrid loaders combine the benefits of both hydraulic and electric systems. These machines offer flexibility by using electric power for routine operations and hydraulic power when additional strength is needed. This combination can optimize energy use and provide the best of both worlds—efficiency and power. Hybrid loaders are designed to meet diverse operational needs and are often seen as a future-proof option due to their adaptability and reduced environmental impact.
Choosing the Right Type for Your Needs
Cargo Type and Volume: The type of cargo you handle plays a significant role in determining the right loader for your operations. For instance, if you frequently manage heavy or bulk materials, a hydraulic loader’s high lifting capacity will be advantageous. On the other hand, if your cargo is lighter and you need a quieter, more eco-friendly solution, an electric or hybrid loader may be more appropriate. Assess the typical cargo types and volumes you deal with to make an informed choice.
Port Infrastructure: Your port’s existing infrastructure can influence which type of mobile vessel loader is best suited for your operations. Consider factors such as space availability, power supply, and access to maintenance facilities. For example, electric loaders require a reliable power source and adequate charging infrastructure, while hydraulic loaders need sufficient space for their larger components and maintenance requirements. Aligning the loader type with your port’s infrastructure ensures seamless integration and efficient operation.
Operational Requirements: Evaluate the specific needs of your port operations, including the frequency of use, duration of operations, and any special requirements. If your operations involve continuous and high-intensity cargo handling, a hydraulic loader’s robust performance may be necessary. For ports with varied or less demanding tasks, an electric or hybrid loader could offer sufficient capability with added benefits such as lower noise levels and reduced emissions. Understanding your operational demands will help you select a loader that enhances efficiency and meets your requirements.
In summary, understanding the different types of mobile vessel loaders—hydraulic, electric, and hybrid—can help you make a well-informed decision based on your specific needs. Each type offers unique benefits, and by aligning these with your cargo type, port infrastructure, and operational requirements, you can choose the right loader to optimize your port operations.
Key Features to Look for in a Mobile Vessel Loader
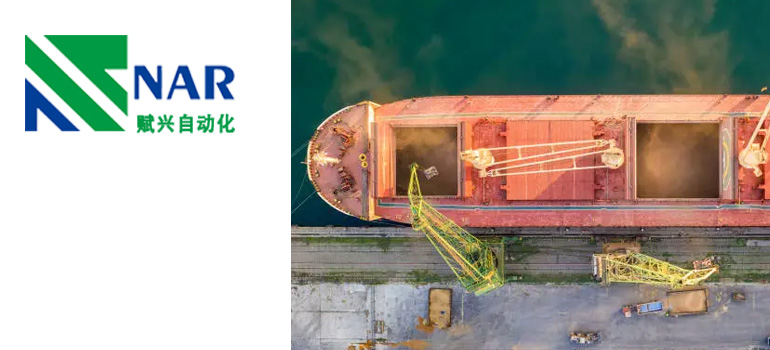
Selecting the right mobile vessel loader for your port operations involves evaluating several key features that can impact efficiency, safety, and overall performance. Here’s a detailed look at the essential features to consider when choosing a mobile vessel loader:
Load Capacity and Reach
Maximum Load Capacity: One of the most critical factors to consider is the load capacity of the mobile vessel loader. The loader must be able to handle the maximum weight of the cargo you plan to move. Ensure that the loader’s specifications meet or exceed your typical cargo requirements. A higher load capacity provides greater flexibility and efficiency in handling heavier or larger cargo, reducing the need for multiple lifts and minimizing turnaround time.
Reach and Maneuverability: The reach of the loader is crucial for accessing different areas of a vessel and for loading/unloading cargo efficiently. Assess the loader’s boom length and extension capabilities to ensure it can reach all necessary parts of the vessel. Additionally, consider the loader’s maneuverability, including its turning radius and ability to operate in confined spaces. A loader with good reach and maneuverability can improve operational efficiency and reduce delays.
Stability and Safety Features: Stability is essential for safe operation, especially when handling heavy or oversized loads. Look for loaders equipped with stability features such as outriggers or stabilizers that enhance balance and prevent tipping. Safety features like load moment indicators (LMIs) and automatic overload protection can help prevent accidents and ensure that the loader operates within its safe limits. Proper stability and safety features are crucial for protecting both the equipment and personnel.
Ease of Use and Maintenance
Operator Training Requirements: A user-friendly control system can significantly impact the ease of operation and reduce the learning curve for new operators. Look for loaders with intuitive controls and interfaces that simplify operation. Additionally, consider the availability of training programs or resources provided by the manufacturer to ensure that operators can quickly become proficient with the equipment.
Maintenance Accessibility: Efficient maintenance is essential for keeping the loader in good working condition and minimizing downtime. Evaluate how easy it is to access critical components for routine maintenance tasks, such as checking fluid levels, replacing filters, or performing inspections. Loaders designed with accessible maintenance points and clear service instructions can help streamline upkeep and extend the equipment’s lifespan.
User-Friendly Controls: Modern mobile vessel loaders often come with advanced control systems that enhance operational efficiency. Look for features such as joystick controls, digital displays, and programmable settings that allow for precise and efficient operation. User-friendly controls can improve productivity and reduce the risk of operator error.
Environmental and Safety Considerations
Emission Levels: Environmental regulations are increasingly focusing on reducing emissions from port operations. If your port has strict environmental standards, consider a loader with low emissions or alternative power sources, such as electric or hybrid models. These loaders produce fewer pollutants and can help your operation comply with environmental regulations while contributing to a cleaner port environment.
Safety Features: Safety should be a top priority when selecting a mobile vessel loader. Look for features such as automatic shut-off systems, emergency stop buttons, and warning alarms that alert operators to potential hazards. Additionally, consider the inclusion of safety lights, cameras, and sensors that provide better visibility and prevent accidents.
Noise Levels: Noise pollution can be a concern in busy port environments. Choose a loader with low noise levels to minimize disruption and comply with local noise regulations. Electric and hybrid loaders typically offer quieter operation compared to diesel-powered models, making them a suitable choice for noise-sensitive areas.
In summary, when selecting a mobile vessel loader, consider key features such as load capacity, reach, stability, ease of use, and maintenance. Additionally, pay attention to environmental and safety considerations to ensure that the loader meets your operational needs while adhering to regulations and promoting a safe working environment.
Cost Factors and Budgeting for a Mobile Vessel Loader
When investing in a mobile vessel loader, understanding the cost factors and budgeting appropriately are crucial steps to ensure that you make a financially sound decision. Here’s an in-depth look at the various cost considerations and budgeting tips for acquiring a mobile vessel loader:
Initial Investment vs. Long-Term Costs
Upfront Purchase Price: The initial purchase price of a mobile vessel loader can vary significantly based on its type, size, and features. Hydraulic loaders, electric loaders, and hybrid models each have different price points due to their distinct technologies and capabilities. It’s important to compare quotes from multiple suppliers and consider factors such as warranty coverage and included services. While a higher initial cost might seem daunting, it’s often reflective of better performance and longer-term durability.
Operating Costs: Beyond the initial investment, operating costs play a significant role in the total cost of ownership. Key components include fuel or electricity costs, depending on the type of loader. Diesel-powered hydraulic loaders may have higher fuel expenses compared to electric or hybrid models. Additionally, regular maintenance, such as servicing, repairs, and part replacements, will contribute to ongoing expenses. Evaluate these costs to understand how they impact your overall budget and operational efficiency.
Potential for Cost Savings: Investing in a higher-quality or more advanced loader can lead to potential cost savings over time. For example, loaders with better fuel efficiency or lower maintenance requirements may reduce operational costs. Moreover, enhanced efficiency and productivity can lead to faster cargo handling, which can translate to increased throughput and revenue. Assess the potential long-term savings and weigh them against the initial investment to make a balanced decision.
Financing Options and Budget Planning
Leasing vs. Buying: When considering financing options, you’ll need to decide between leasing and buying the mobile vessel loader. Leasing can provide lower upfront costs and flexibility, as you can upgrade to newer models more frequently. However, it may result in higher long-term costs if you lease for extended periods. Buying offers ownership benefits and can be more cost-effective in the long run, especially if the loader is used extensively. Evaluate your financial situation and operational needs to determine which option aligns best with your budget.
Financing Options: Explore various financing options available for acquiring a mobile vessel loader. These may include equipment loans, leasing agreements, or manufacturer financing programs. Equipment loans typically offer lower interest rates and allow you to spread the cost over several years. Leasing agreements can provide flexibility and lower initial costs but may come with higher total expenses. Investigate each option thoroughly and choose the one that fits your budget and financial goals.
Budget Allocation: Proper budget allocation is essential for managing the total cost of ownership. Besides the purchase or lease price, allocate funds for ancillary expenses such as delivery, installation, and operator training. Ensure that your budget covers these additional costs to avoid unexpected financial strain. Additionally, set aside a contingency fund for unforeseen repairs or maintenance needs. Planning your budget comprehensively will help you manage expenses effectively and ensure a smooth acquisition process.
Return on Investment (ROI)
Measuring ROI: Assessing the return on investment (ROI) involves evaluating how the mobile vessel loader contributes to your overall financial performance. Key metrics to track include improvements in operational efficiency, reductions in labor costs, and increased cargo throughput. Calculate the ROI by comparing the loader’s impact on productivity and cost savings against its initial and ongoing expenses.
Improved Efficiency: A high-quality mobile vessel loader can significantly enhance operational efficiency. Faster cargo handling, reduced downtime, and smoother operations all contribute to increased productivity. Quantify these improvements in terms of time saved and additional revenue generated to understand the loader’s impact on your bottom line.
Increased Throughput: One of the primary benefits of investing in a mobile vessel loader is the potential for increased cargo throughput. By handling more cargo efficiently, you can boost your port’s capacity and potentially attract more business. Analyze the loader’s effect on throughput and its contribution to overall revenue growth.
In summary, when budgeting for a mobile vessel loader, consider the initial investment, ongoing operating costs, and potential cost savings. Evaluate financing options, allocate your budget effectively, and assess the return on investment to make an informed and financially sound decision. Proper planning and analysis will help you optimize your investment and achieve long-term operational success.
Assessing the Supplier and Support Services
When investing in a mobile vessel loader, evaluating the supplier and the support services they offer is crucial for ensuring a smooth acquisition and ongoing operation. A reliable supplier and robust support services can significantly impact the performance, maintenance, and overall satisfaction with your equipment. Here’s how to assess these factors effectively:
Evaluating Supplier Reputation and Reliability
Supplier Reviews and Ratings: Begin by researching the supplier’s reputation through reviews and ratings from previous customers. Look for feedback on their website, industry forums, and third-party review sites. Positive reviews and high ratings generally indicate a trustworthy supplier with a history of satisfying customers. Pay attention to specific comments about the supplier’s responsiveness, product quality, and after-sales service.
Years in Business: The length of time a supplier has been in business can be a good indicator of their reliability and experience. Suppliers with a long track record are often more established and better equipped to handle customer needs. They are likely to have more experience with various types of equipment and be better at resolving issues quickly. Consider choosing a supplier with a proven history in the industry to ensure reliability and stability.
Customer Support: Assess the level of customer support provided by the supplier. Reliable suppliers offer comprehensive support before, during, and after the purchase. This includes clear communication channels, responsive customer service, and assistance with any issues that may arise. A supplier that prioritizes customer support is more likely to address problems efficiently and provide valuable guidance throughout the equipment’s lifecycle.
Warranty and Service Agreements
Standard Warranty Terms: Review the standard warranty terms offered with the mobile vessel loader. A solid warranty should cover key components and protect against defects in materials and workmanship. Check the duration of the warranty and any exclusions or limitations. A longer warranty period often reflects the supplier’s confidence in their product and provides added peace of mind.
Extended Service Agreements: Consider whether the supplier offers extended service agreements beyond the standard warranty. Extended agreements can provide additional coverage for wear and tear, routine maintenance, and repairs. These agreements can be beneficial for long-term cost management and ensure that you have access to support and parts as needed.
Emergency Support: Evaluate the supplier’s ability to provide emergency support in case of unexpected breakdowns or urgent issues. Prompt response times and accessible support are essential to minimize downtime and keep your operations running smoothly. Check if the supplier offers 24/7 support or emergency service options and ensure that their service network is well-established and capable of addressing urgent needs quickly.
Spare Parts and After-Sales Service
Availability of Spare Parts: Ensure that the supplier provides easy access to spare parts for the mobile vessel loader. The availability of parts is crucial for maintaining the equipment and addressing any issues that may arise. Verify that the supplier has a reliable supply chain for parts and that they can deliver them promptly when needed.
Service Network: Investigate the supplier’s service network to determine the availability of local technicians and service centers. A robust service network can provide timely repairs and maintenance, reducing downtime and operational disruptions. Choose a supplier with a well-established network or partnerships with local service providers to ensure convenient and efficient support.
After-Sales Support: Consider the quality of after-sales support provided by the supplier. This includes ongoing assistance, technical support, and training for operators. Good after-sales support can enhance your experience with the equipment and help you maximize its potential. Ensure that the supplier offers training resources, technical documentation, and responsive support to address any questions or concerns you may have.
In summary, assessing the supplier and support services involves evaluating the supplier’s reputation, customer reviews, warranty terms, and service agreements. Additionally, consider the availability of spare parts, the strength of the service network, and the quality of after-sales support. By thoroughly assessing these factors, you can ensure that you choose a reliable supplier and receive the support needed to keep your mobile vessel loader operating efficiently and effectively.