Summary:
Boosting Accuracy and Speed: Dynamic Weighing in Modern Production
Processes Understanding the Evolution of Weighing Technologies
Importance of Accuracy and Speed in Modern Production Processes
Advantages of Dynamic Weighing Systems
Future Trends and Innovations in Dynamic Weighing
The emergence of dynamic weighing technology marks an important step for the production industry towards a more intelligent and efficient direction. It not only provides accurate weight measurement, but more importantly, real-time monitoring of product quality and quantity during the production process. The availability of real-time data enables production managers to make decisions more quickly, optimize production processes, and improve production efficiency.
Processes Understanding the Evolution of Weighing Technologies
Weighing technologies have undergone a remarkable evolution over the years, transforming from simple manual scales to highly sophisticated dynamic weighing systems used in modern production environments. This evolution has been driven by the need for greater accuracy, efficiency, and automation in various industries.
A Journey Through Time
The journey of weighing technologies begins centuries ago with the invention of rudimentary balance scales used by ancient civilizations for trade and commerce. These early scales relied on basic principles of physics to measure weight but lacked precision and consistency.
As time progressed, the Industrial Revolution brought significant advancements to weighing technology. Mechanical scales were developed, incorporating gears, levers, and springs to achieve more accurate measurements. These scales revolutionized industries such as agriculture, manufacturing, and transportation, enabling greater efficiency and standardization in trade.
The Advent of Electronic Weighing
The latter half of the 20th century witnessed a paradigm shift with the introduction of electronic weighing systems. Unlike their mechanical counterparts, electronic scales utilized sensors and transducers to convert weight into electrical signals, offering unparalleled accuracy and reliability.
The miniaturization of electronic components and the advent of microprocessors further revolutionized weighing technology, paving the way for digital scales and precision instruments capable of measuring weights down to the milligram.
Dynamic Weighing: A New Era
In recent decades, dynamic weighing has emerged as a cutting-edge technology poised to redefine weighing processes in modern production settings. Unlike static weighing, which involves measuring stationary objects, dynamic weighing encompasses the measurement of moving objects in real-time.
Dynamic weighing systems utilize advanced sensors, signal processing algorithms, and automation technologies to accurately measure weights while items are in motion. This capability has revolutionized industries such as food processing, pharmaceuticals, and logistics, where high-speed production lines demand rapid and precise weight measurements.
Looking Ahead
As we look to the future, the evolution of weighing technologies shows no signs of slowing down. Advancements in materials science, sensor technology, and data analytics are driving innovation in areas such as wireless weighing, IoT integration, and predictive maintenance.
By understanding the rich history and ongoing evolution of weighing technologies, we can appreciate the strides made in enhancing accuracy, efficiency, and productivity across diverse industries. From ancient balance scales to state-of-the-art dynamic weighing systems, the journey of weighing technology underscores humanity’s quest for precision and progress.
Importance of Accuracy and Speed in Modern Production Processes
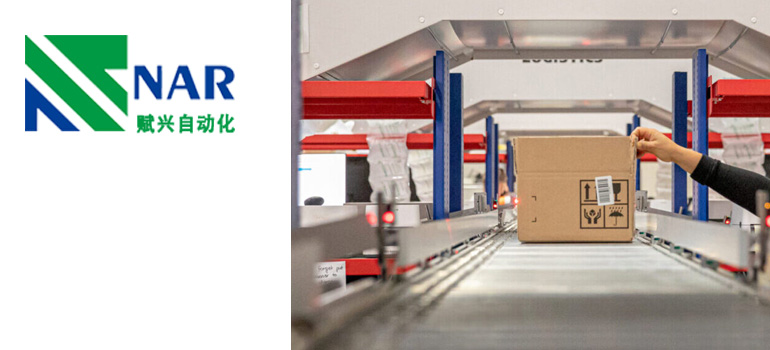
In today’s fast-paced and competitive business landscape, the importance of accuracy and speed in modern production processes cannot be overstated. These two factors are not only crucial for meeting customer demands and staying ahead of the competition but also for ensuring operational efficiency, minimizing costs, and maximizing profitability.
Enhancing Product Quality
Accuracy plays a pivotal role in maintaining product quality standards. In industries such as manufacturing, automotive, electronics, and pharmaceuticals, even the slightest deviation in measurements can lead to defects, rework, or product recalls. By ensuring precise measurements and adherence to specifications, businesses can deliver products that meet or exceed customer expectations, thereby enhancing brand reputation and customer satisfaction.
Meeting Tight Deadlines
Speed is equally essential in modern production processes, where time-to-market can make or break a company’s success. With consumers expecting rapid delivery of goods and services, manufacturers must streamline their operations to meet tight deadlines without compromising quality. High-speed production lines equipped with advanced automation and robotics enable faster throughput, reducing cycle times and improving overall efficiency.
Driving Operational Efficiency
The synergy between accuracy and speed is central to driving operational efficiency across the entire production ecosystem. By optimizing processes, minimizing waste, and reducing downtime, businesses can maximize resource utilization and yield higher returns on investment. Real-time monitoring and data analytics further empower organizations to identify bottlenecks, fine-tune workflows, and make informed decisions to enhance productivity and profitability.
Adapting to Market Dynamics
In today’s dynamic marketplace, agility is paramount for staying competitive and responsive to changing customer needs and market trends. Production processes must be agile enough to scale up or down quickly, accommodate customizations, and adapt to fluctuations in demand. By integrating flexible manufacturing systems and agile methodologies, businesses can gain a competitive edge, capitalize on emerging opportunities, and mitigate risks effectively.
In conclusion, the importance of accuracy and speed in modern production processes cannot be underestimated. By prioritizing precision and efficiency, businesses can achieve higher levels of quality, productivity, and customer satisfaction. Whether it’s delivering flawless products, meeting tight deadlines, driving operational excellence, or adapting to market dynamics, accuracy and speed are the cornerstones of success in today’s rapidly evolving business landscape.
Advantages of Dynamic Weighing Systems
Dynamic weighing systems offer a host of advantages that make them indispensable tools in modern production environments. From enhancing accuracy and efficiency to enabling real-time monitoring and optimization, these systems revolutionize the way goods are processed, packaged, and delivered. Below are some key advantages of dynamic weighing systems:
Enhanced Accuracy and Precision
Dynamic weighing systems utilize advanced sensors and algorithms to measure weights with unparalleled accuracy, even while items are in motion. This level of precision ensures that products meet stringent quality standards and regulatory requirements, minimizing errors, rework, and product waste. By providing precise measurements, dynamic weighing systems contribute to higher product consistency and customer satisfaction.
Increased Efficiency and Throughput
One of the most significant advantages of dynamic weighing systems is their ability to boost production efficiency and throughput. By integrating seamlessly into production lines, these systems enable continuous weight monitoring and sorting of items at high speeds. This streamlined process minimizes bottlenecks, reduces cycle times, and maximizes equipment utilization, ultimately leading to higher output and lower operational costs.
Real-Time Data Insights
Dynamic weighing systems provide real-time data insights that empower production managers to make informed decisions on the fly. By monitoring weight variations and trends in real-time, managers can identify issues, adjust settings, and optimize production parameters to maintain peak performance. This proactive approach minimizes downtime, prevents quality defects, and ensures smooth operation of production lines.
Flexibility and Adaptability
Dynamic weighing systems offer unparalleled flexibility and adaptability to accommodate diverse products, packaging formats, and production requirements. Whether dealing with variable weights, shapes, or sizes, these systems can adjust dynamically to ensure accurate measurement and sorting. This versatility makes dynamic weighing systems ideal for industries with changing product lines or seasonal fluctuations in demand.
Improved Productivity and ROI
By optimizing weighing processes and minimizing manual intervention, dynamic weighing systems contribute to improved productivity and return on investment (ROI). The automation of repetitive tasks reduces labor costs and human error while maximizing throughput and yield. Additionally, the enhanced accuracy and efficiency provided by these systems translate into higher-quality products and increased customer satisfaction, further driving profitability.
In conclusion, dynamic weighing systems offer a myriad of advantages that are indispensable for modern production environments. From enhancing accuracy and efficiency to providing real-time data insights and flexibility, these systems empower businesses to optimize their operations, maximize productivity, and deliver high-quality products to market. As industries continue to evolve, dynamic weighing systems will remain essential tools for driving innovation, competitiveness, and success.
Future Trends and Innovations in Dynamic Weighing
Dynamic weighing technology has already revolutionized production processes across various industries, but the journey of innovation is far from over. As technology continues to advance and market demands evolve, several key trends and innovations are poised to shape the future of dynamic weighing. Here are some insights into what lies ahead:
Integration with IoT and Industry 4.0
One of the most significant trends in dynamic weighing is its integration with the Internet of Things (IoT) and the principles of Industry 4.0. By connecting dynamic weighing systems to a network of sensors, actuators, and cloud-based platforms, manufacturers can create smart, interconnected production environments. Real-time data from dynamic weighing systems can be leveraged to optimize processes, predict maintenance needs, and enable proactive decision-making for greater efficiency and reliability.
Advancements in Sensor Technology
The future of dynamic weighing will be shaped by advancements in sensor technology, particularly in the development of more accurate, reliable, and versatile sensors. Emerging technologies such as advanced imaging, laser scanning, and artificial intelligence (AI) will enable dynamic weighing systems to measure weights with unprecedented precision, even in challenging environments. These advancements will open up new possibilities for applications in industries such as food processing, logistics, and pharmaceuticals.
Enhanced Automation and Robotics
Automation and robotics will play a pivotal role in the future of dynamic weighing, enabling greater speed, accuracy, and efficiency in production processes. Robotic arms equipped with integrated weighing sensors will streamline material handling and sorting tasks, reducing reliance on manual labor and minimizing errors. Autonomous mobile robots (AMRs) equipped with dynamic weighing capabilities will further enhance flexibility and adaptability in warehouse and logistics operations.
Blockchain Integration for Supply Chain Traceability
Blockchain technology holds the potential to revolutionize supply chain management by providing transparent, immutable records of product provenance and movement. In the context of dynamic weighing, blockchain integration can enhance traceability and accountability throughout the production process. By recording weight measurements and other relevant data on a blockchain ledger, manufacturers can ensure the integrity and authenticity of their products, thereby building trust with consumers and stakeholders.
Sustainability and Green Technologies
As sustainability becomes increasingly important for businesses and consumers alike, the future of dynamic weighing will see a greater emphasis on green technologies and eco-friendly practices. Energy-efficient weighing systems, recyclable materials, and reduced packaging waste will be key priorities for manufacturers seeking to minimize their environmental footprint. Dynamic weighing systems will play a vital role in optimizing resource utilization, reducing waste, and promoting sustainable production practices.
In conclusion, the future of dynamic weighing holds immense promise for driving innovation, efficiency, and sustainability in production processes. By embracing trends such as IoT integration, sensor advancements, automation, blockchain traceability, and sustainability initiatives, manufacturers can stay ahead of the curve and unlock new opportunities for growth and competitiveness. Dynamic weighing will continue to evolve as a critical enabler of smart, agile, and environmentally conscious manufacturing operations in the years to come.