Summary:
The Future of Manufacturing: Harnessing Automatic Material Conveyors
What is Automatic Material Conveyors?
Evolution of Material Conveyors
Components and Types of Automatic Material Conveyors
The Advantages of Automatic Material Conveyors
What is Automatic Material Conveyors?
Automatic Material Conveyors refers to the process of transporting goods, raw materials, or products from one location to another within a manufacturing facility, warehouse, distribution center, or any other industrial setting. It is a fundamental aspect of logistics and plays a crucial role in ensuring smooth and efficient operations in various industries.
Automatic Material Conveyors can involve the movement of items over short or long distances and can be achieved through a variety of methods, including manual labor, mechanical devices, and automated systems. The primary goal of material conveyance is to streamline the flow of materials, reduce handling costs, minimize errors, and optimize production processes.
Key components of material conveyor systems may include conveyors, chutes, lifts, hoists, automated guided vehicles (AGVs), and robotics. These components work together to move materials safely, reliably, and efficiently throughout a facility.
Overall, material conveyor is essential for facilitating the movement of goods within industrial environments, enabling businesses to meet production schedules, fulfill orders, and maintain high levels of productivity.
Evolution of Material Conveyors
The evolution of material conveyors has been a fascinating journey, marked by innovation, technological advancements, and the quest for efficiency in material handling processes. Here’s an overview of the key stages in the evolution of material conveyors:
Early Conveyance Methods:
Primitive Conveyance Systems: Early humans used basic methods like carrying items by hand or on rudimentary platforms to move materials over short distances.
Ancient Civilizations: Ancient civilizations such as the Egyptians and Greeks employed simple devices like ramps and sledges for transporting heavy loads in construction and agriculture.
Industrial Revolution and Mechanization:
Introduction of Mechanical Conveyors: With the onset of the Industrial Revolution in the 18th century, mechanized conveyors began to emerge, driven by steam power.
Belt and Chain Conveyors: Innovations like belt conveyors and chain conveyors revolutionized material handling in factories and mines, enabling the efficient movement of bulk materials over longer distances.
Electrification and Automation:
Electrically Powered Conveyors: The advent of electricity in the late 19th and early 20th centuries led to the widespread adoption of electrically powered conveyors, enhancing speed and reliability.
Automated Conveyor Systems: In the mid-20th century, automated conveyor systems with programmable controls and sensors started to gain traction, offering increased efficiency and flexibility in material handling operations.
Technological Advancements:
Integration of Robotics: Modern material handling systems leverage robotics and automation technologies for tasks such as sorting, palletizing, and packaging, improving accuracy and throughput.
Advancements in Conveyor Design: Continuous advancements in conveyor design, including modular components, lightweight materials, and energy-efficient drive systems, have further optimized performance and sustainability.
Industry 4.0 and Beyond:
Digitalization and Connectivity: The emergence of Industry 4.0 technologies, such as the Internet of Things (IoT) and data analytics, is transforming material conveyance by enabling real-time monitoring, predictive maintenance, and adaptive control.
Flexible and Agile Systems: Future trends in material conveyance focus on developing more flexible, agile, and responsive systems capable of handling diverse products, adapting to changing production demands, and integrating seamlessly with smart manufacturing environments.
The evolution of material conveyors underscores the relentless pursuit of efficiency, safety, and productivity in industrial operations, driving continuous innovation and technological progress in the field of material handling.
Components and Types of Automatic Material Conveyors
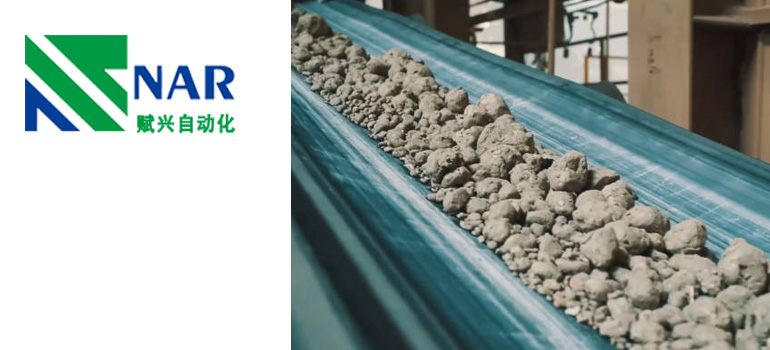
Certainly, let’s delve into the components and types of automatic material conveyors:
Basic Components of Automatic Material Conveyors:
Conveyor Belt:
Function: The conveyor belt serves as the primary surface for transporting materials.
Materials: Constructed from various materials such as rubber, PVC, or metal, depending on the application.
Drive Unit:
Function: Provides the power necessary to move the conveyor belt.
Types: Electric motors, hydraulic systems, or pneumatic systems may drive the conveyor belt.
Idlers and Rollers:
Function: Support the conveyor belt and facilitate its movement.
Types: Includes idler rollers, return rollers, and impact rollers.
Pulleys:
Function: Redirect the conveyor belt and provide tension to maintain proper alignment.
Types: Head pulley, tail pulley, and bend pulley.
Control System:
Function: Regulates the speed, direction, and operation of the conveyor system.
Components: PLC (Programmable Logic Controller), sensors, switches, and HMI (Human-Machine Interface).
Types of Automatic Material Conveyors:
Belt Conveyors:
Description: Consist of a continuous loop of material-carrying conveyor belt.
Applications: Suitable for transporting bulk materials, packages, and irregularly shaped items.
Roller Conveyors:
Description: Utilize rollers mounted on a frame to transport materials.
Types: Gravity roller conveyors and powered roller conveyors.
Chain Conveyors:
Description: Feature a chain-driven mechanism to move materials along the conveyor.
Applications: Ideal for heavy-duty applications and handling pallets or large items.
Screw Conveyors:
Description: Utilize a rotating screw mechanism to move materials along a trough or tube.
Applications: Commonly used for transporting bulk materials, powders, and granular materials.
Overhead Conveyors:
Description: Suspended from the ceiling or mounted on an elevated track system.
Applications: Suitable for space-saving applications, such as paint lines or assembly lines.
Pneumatic Conveyors:
Description: Use air pressure to transport materials through a pipeline or duct.
Applications: Often used for transporting powdered or granular materials in industries like food processing and pharmaceuticals.
Automatic material conveyors come in various types and configurations, each designed to meet specific material handling needs and operational requirements. By understanding the components and types available, businesses can choose the most suitable conveyor system to optimize their material handling processes.
The Advantages of Automatic Material Conveyors
Certainly, let’s explore the advantages of automatic material conveyors:
Enhanced Efficiency:
Continuous Operation: Automatic material conveyors operate continuously, minimizing downtime and maximizing throughput.
Consistent Speed and Accuracy: Automated systems ensure consistent material movement, reducing errors and improving production efficiency.
Optimized Workflow: Streamlined material handling processes result in smoother operations and faster turnaround times.
Improved Safety:
Reduced Manual Handling: Automatic conveyors minimize the need for manual material handling, reducing the risk of worker injuries associated with lifting and carrying heavy loads.
Integrated Safety Features: Modern automatic conveyor systems are equipped with safety sensors, emergency stop buttons, and protective guards to enhance workplace safety.
Cost Savings:
Labor Savings: By automating material handling tasks, businesses can reduce labor costs associated with manual labor and repetitive tasks.
Increased Productivity: Improved efficiency and throughput lead to higher productivity levels, allowing businesses to achieve more with fewer resources.
Reduced Material Loss: Automated systems minimize material damage and loss during handling, resulting in cost savings and improved product quality.
Flexibility and Scalability:
Adaptable Configurations: Automatic material conveyors can be customized to accommodate various layouts, production requirements, and material types.
Scalable Solutions: As business needs evolve, automated conveyor systems can be easily expanded or modified to meet changing demands, providing scalability and future-proofing.
Quality Control:
Consistent Handling: Automated systems ensure consistent material handling practices, reducing the risk of product damage or contamination.
Traceability and Monitoring: Integrated control systems allow for real-time monitoring of material flow, enabling better traceability and quality control throughout the production process.
Environmental Benefits:
Energy Efficiency: Some automatic conveyors feature energy-efficient designs and technologies, reducing energy consumption and environmental impact.
Waste Reduction: By minimizing material waste and optimizing processes, automated systems contribute to sustainable manufacturing practices and resource conservation.
Automatic material conveyors offer numerous advantages, including enhanced efficiency, improved safety, cost savings, flexibility, quality control, and environmental benefits. By leveraging automated conveyor systems, businesses can optimize their material handling processes, increase productivity, and gain a competitive edge in today’s fast-paced industrial environment.
Maybe you are interested in the following: Optimizing Workflow: How Industrial Conveyors Boost Productivity