Summary:
5 Key Advantages of Industrial Belt Conveyors Over Traditional Systems
Enhanced Efficiency with Industrial Belt Conveyors
Superior Durability of Industrial Belt Conveyors
Customization and Flexibility of Industrial Belt Conveyor Systems
Safety and Environmental Benefits of Industrial Belt Conveyors
Cost-Effectiveness of Industrial Belt Conveyors
Enhanced Efficiency with Industrial Belt Conveyors
In today’s fast-paced manufacturing and logistics industries, efficiency is key to staying competitive. Industrial belt conveyors have become an essential tool for businesses looking to improve productivity and reduce operational costs. Compared to traditional material handling methods, industrial belt conveyors offer significant advantages in terms of speed, automation, and throughput.
Faster Material Handling Processes
One of the primary benefits of industrial belt conveyors is their ability to dramatically speed up material handling processes. Traditional systems often rely on manual labor or slower, less efficient machinery. In contrast, industrial belt conveyors can continuously and smoothly transport large volumes of materials, whether heavy-duty items, bulk goods, or delicate components. This ensures that materials are moved quickly from one point to another, minimizing downtime and delays in the production line.
This faster handling not only increases the speed of the production process but also ensures smoother logistics and reduces the time products spend in transit. In high-demand manufacturing environments, such as automotive or electronics production, faster material handling is crucial to maintaining a steady flow and meeting tight deadlines.
Reducing Labor Costs with Automated Systems
Industrial belt conveyors are often paired with automated control systems, which significantly reduce the need for manual labor. In traditional systems, workers are required to manually handle materials, sort items, and transport goods from one stage of production to another. This can lead to high labor costs, inefficiencies, and the potential for human error.
With automated conveyor systems, these tasks are handled seamlessly without the need for constant human supervision. Conveyors run 24/7 with minimal interruptions, and employees can focus on more specialized tasks such as machine maintenance or quality control. This shift towards automation not only reduces labor costs but also improves the overall accuracy and reliability of the production process.
Increased Throughput in Manufacturing Operations
By integrating industrial belt conveyors into a production line, businesses can achieve higher throughput levels. Traditional conveyor systems are often limited by speed and capacity, whereas modern industrial belt conveyors can be customized to handle higher speeds and greater loads. This ability to scale up operations means that businesses can produce more products in the same amount of time, meeting increased demand without compromising efficiency.
Higher throughput doesn’t just mean producing more goods; it also allows companies to fulfill larger orders, meet tighter delivery deadlines, and maintain consistent production quality. For industries that require high-volume output—such as food processing, packaging, or material handling—industrial belt conveyors are a game-changer in terms of productivity and operational efficiency.
Superior Durability of Industrial Belt Conveyors
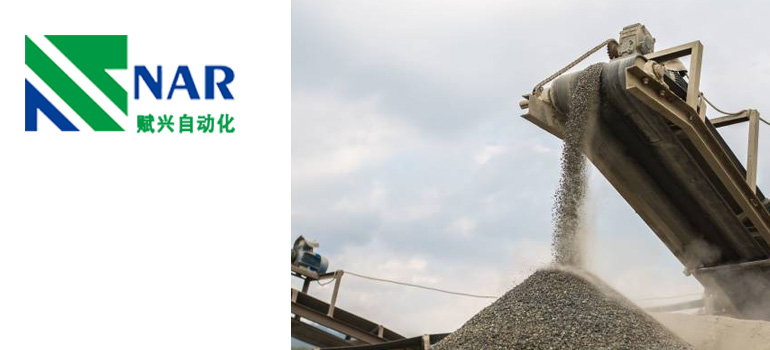
When it comes to material handling systems, durability is a critical factor that directly impacts the reliability and longevity of operations. Industrial belt conveyors are built to last, offering superior durability compared to traditional conveyor systems. Their robust construction, ability to withstand heavy loads, and resistance to wear and tear make them a reliable choice for businesses in demanding industries like mining, manufacturing, and logistics.
Heavy-Duty Materials for Harsh Environments
One of the key advantages of industrial belt conveyors is their ability to handle tough working conditions. These conveyors are typically made from heavy-duty materials such as steel, reinforced rubber, and advanced synthetic composites that can endure extreme environments. Whether it’s high temperatures, heavy loads, abrasive materials, or exposure to chemicals, industrial belt conveyors are designed to withstand it all. This makes them ideal for industries such as mining, cement production, and recycling, where conveyors are exposed to harsh operational conditions day in and day out.
Unlike traditional conveyor systems, which may require frequent repairs or replacements due to material fatigue, industrial belt conveyors are engineered to endure for long periods with minimal maintenance. This durability reduces downtime and increases overall system reliability, ensuring that production processes remain smooth and uninterrupted.
Longer Lifespan Compared to Traditional Conveyors
The lifespan of industrial belt conveyors is significantly longer than that of traditional systems. Traditional conveyors often suffer from frequent mechanical breakdowns, especially when subjected to continuous operation or harsh conditions. Over time, components such as rollers, belts, and pulleys wear down, leading to costly repairs and replacement.
Industrial belt conveyors, on the other hand, are built with longevity in mind. With features like self-aligning idlers, durable pulleys, and high-tensile strength belts, these conveyors are designed to perform for years without the need for constant maintenance. This extended lifespan not only reduces the frequency of replacements but also lowers long-term operating costs. For businesses looking to make a long-term investment, industrial belt conveyors provide a cost-effective solution that pays off in the form of fewer disruptions and better ROI.
Reduced Wear and Tear on Machinery
Another advantage of industrial belt conveyors is their ability to reduce wear and tear on other machinery in the production process. Traditional conveyor systems often place significant stress on both the materials being transported and the equipment itself. This can result in frequent breakdowns or the need for excessive maintenance.
Industrial belt conveyors, however, are designed to distribute the load evenly across the system, reducing friction and minimizing the strain on other components. With features like shock absorbers, advanced belt tensioning systems, and high-quality rollers, these conveyors ensure smooth operation with less stress on the system. This not only extends the lifespan of the conveyor itself but also helps protect other machinery and equipment from unnecessary wear, further contributing to overall operational efficiency.
Customization and Flexibility of Industrial Belt Conveyor Systems
One of the standout features of industrial belt conveyors is their remarkable customization and flexibility. Unlike traditional conveyor systems, which may come with fixed specifications, industrial belt conveyors can be tailored to meet the unique needs of different industries and operational requirements. This adaptability allows businesses to design conveyor systems that are perfectly suited to their workflows, improving efficiency, reducing bottlenecks, and optimizing overall performance.
Tailored Conveyor Belt Designs for Different Industries
Industrial belt conveyors are highly customizable, which makes them an ideal solution for a wide range of industries. Whether you’re working in food processing, automotive manufacturing, mining, or pharmaceuticals, there is a conveyor design that can meet your specific needs. Conveyor belts can be designed with different materials, widths, lengths, and capacities depending on the type of materials being transported.
For example, in food processing, conveyors may need to meet strict hygiene standards, so belts made from food-grade materials like stainless steel or FDA-approved rubber are commonly used. In industries that handle bulk materials, such as mining or agriculture, conveyors may be designed with reinforced belts or additional sidewalls to prevent spillage. The ability to design a conveyor that matches the unique demands of your operation is a key factor in maximizing productivity and ensuring safe, efficient handling of materials.
Adapting Conveyor Lengths and Widths for Specific Needs
Another important aspect of industrial belt conveyors is their ability to be customized in terms of size—both length and width. Depending on the layout of your factory or warehouse, conveyors can be adjusted to fit available space while still maintaining high efficiency. Whether you need a short, compact conveyor for a small workstation or a long conveyor system that stretches across multiple floors, customization options are available to ensure the system works perfectly within your physical environment.
The width of the conveyor belt can also be adjusted to accommodate varying load sizes. For industries that handle irregularly shaped or oversized items, wider belts can provide a more stable and secure transport. By customizing these dimensions, businesses can achieve a streamlined workflow and avoid issues like material spillage or overloading, which could slow down production or lead to system inefficiencies.
Versatility in Conveyor Belt Materials and Components
The flexibility of industrial belt conveyors is further enhanced by the variety of materials and components available for customization. Different belt materials are available depending on the type of materials being transported, the environmental conditions, and specific operational requirements. For instance, in environments where belts may be exposed to high temperatures or abrasive materials, heat-resistant or abrasion-resistant belts can be used.
Furthermore, conveyor components such as pulleys, rollers, and motors can also be selected and customized to fit specific operational needs. Whether you require a motorized pulley for a quieter operation, a specialized roller for handling delicate items, or a heavy-duty pulley for tough material handling, industrial belt conveyors can be configured with the right components to meet the demands of your business. This level of flexibility ensures that your conveyor system can adapt to a wide range of tasks and challenges, making it a future-proof investment for businesses that may need to scale or pivot their operations.
Cost-Effectiveness of Industrial Belt Conveyors
When considering material handling systems, one of the most important factors for businesses is cost-effectiveness. Industrial belt conveyors provide a highly cost-efficient solution for transporting materials, especially when compared to traditional manual labor or other older conveyor systems. From initial installation to long-term operational savings, industrial belt conveyors offer excellent value for the money, making them a preferred choice for many industries looking to optimize their processes and reduce operational costs.
Lower Maintenance Costs Compared to Traditional Systems
One of the most significant cost-saving benefits of industrial belt conveyors is their low maintenance requirement. Traditional conveyors, especially older or less robust systems, often incur high maintenance costs due to frequent breakdowns, wear and tear on parts, and the need for manual intervention. Industrial belt conveyors, however, are designed for durability, with many systems requiring minimal maintenance over their extended lifespan.
Components such as self-aligning rollers, durable belts, and high-quality pulleys are built to last longer, which reduces the frequency of repairs and part replacements. In addition, the design of these conveyors minimizes friction and wear, further extending their service life. By reducing the amount of time spent on maintenance and repairs, businesses can save significantly on labor and parts costs, resulting in lower overall operational expenses.
Reduced Energy Consumption in Industrial Belt Conveyors
Energy efficiency is another area where industrial belt conveyors excel. Traditional conveyor systems may rely on more energy-intensive machinery or manual labor, which can drive up electricity and labor costs. In contrast, modern industrial belt conveyors are designed to operate efficiently, using less energy while still delivering high throughput.
Many industrial belt conveyors are equipped with energy-saving features such as variable-speed drives, which allow businesses to adjust the conveyor’s speed according to demand, optimizing energy use. Additionally, the design of the belts and rollers helps reduce friction, which in turn reduces the energy required to move materials. As energy costs continue to rise, the energy efficiency of industrial belt conveyors can have a significant impact on a business’s bottom line, resulting in long-term savings.
Long-Term Investment Value and ROI
While the initial investment in an industrial belt conveyor system may seem higher than traditional manual methods or less advanced conveyor systems, the long-term value is undeniable. The combination of reduced maintenance costs, energy savings, and increased throughput means that industrial belt conveyors quickly pay for themselves. The ROI (Return on Investment) for businesses that invest in high-quality industrial belt conveyors is typically realized in a short period of time.
Additionally, because these conveyors are built to last and can be customized to meet the specific needs of a business, they offer long-term operational benefits that go beyond the initial purchase price. Businesses can scale their operations without worrying about upgrading or replacing outdated equipment, ensuring a steady and cost-effective operation. Over time, the savings in labor, energy, and maintenance costs far outweigh the initial setup costs, making industrial belt conveyors an excellent investment for businesses of all sizes.
Safety and Environmental Benefits of Industrial Belt Conveyors
In addition to their operational advantages, industrial belt conveyors offer significant safety and environmental benefits that make them a preferred choice for businesses across various industries. With workplace safety and sustainability becoming increasingly important, investing in conveyor systems that enhance both worker safety and environmental impact is a smart and responsible choice. Industrial belt conveyors not only streamline material handling processes but also contribute to safer work environments and greener business operations.
Improved Worker Safety and Reduced Manual Handling
One of the most compelling safety benefits of industrial belt conveyors is their ability to reduce the need for manual labor in material handling. In traditional material handling systems, workers are often required to lift, move, and position heavy or bulky items, putting them at risk for injuries such as strains, sprains, and accidents. Industrial belt conveyors help mitigate these risks by automating the movement of materials, which significantly reduces physical labor and minimizes the chances of workplace injuries.
Conveyors allow materials to be transported efficiently without the need for manual lifting or pushing, leading to a safer and more ergonomic workplace. This shift towards automation not only helps protect employees from physical harm but also promotes a more productive and focused workforce. With fewer work-related injuries, companies can also reduce healthcare costs and lost productivity due to worker downtime, making industrial belt conveyors an essential safety feature for modern workplaces.
Minimizing Environmental Impact with Eco-Friendly Designs
As environmental concerns continue to grow, businesses are increasingly looking for ways to reduce their ecological footprint. Industrial belt conveyors contribute to sustainability efforts by offering more eco-friendly solutions compared to older, less efficient systems. Many modern conveyors are designed with energy-efficient motors, low-friction belts, and recyclable materials, which reduce their overall environmental impact.
The energy-saving features of industrial belt conveyors, such as variable-speed drives, help minimize electricity consumption, contributing to lower carbon emissions. Additionally, the use of durable materials means that conveyor belts last longer and require fewer replacements, reducing the need for manufacturing and transportation of new parts. This results in less waste, fewer raw materials used, and a reduction in the environmental impact associated with producing, transporting, and disposing of conveyor components.
By adopting industrial belt conveyors, businesses can demonstrate their commitment to sustainability, improve their environmental footprint, and align with global efforts to promote greener, more eco-conscious industrial practices.
Compliance with Safety Regulations and Standards
Industrial belt conveyors are designed to meet or exceed safety standards and regulations, ensuring that businesses comply with legal requirements. Conveyor systems used in industries like food processing, mining, and manufacturing must adhere to strict safety and environmental regulations, and industrial belt conveyors are engineered with these guidelines in mind.
Many industrial belt conveyors come equipped with built-in safety features such as emergency stop buttons, guards to prevent accidental contact with moving parts, and sensors that monitor belt tension and alignment. These safety measures help prevent accidents and ensure that employees work in a safe environment. Additionally, compliance with local, national, and international safety standards helps businesses avoid costly fines and potential shutdowns, further emphasizing the value of investing in high-quality, regulated conveyor systems.